CNC Metal Engraving Machine with Automatic Tool Changing Kit
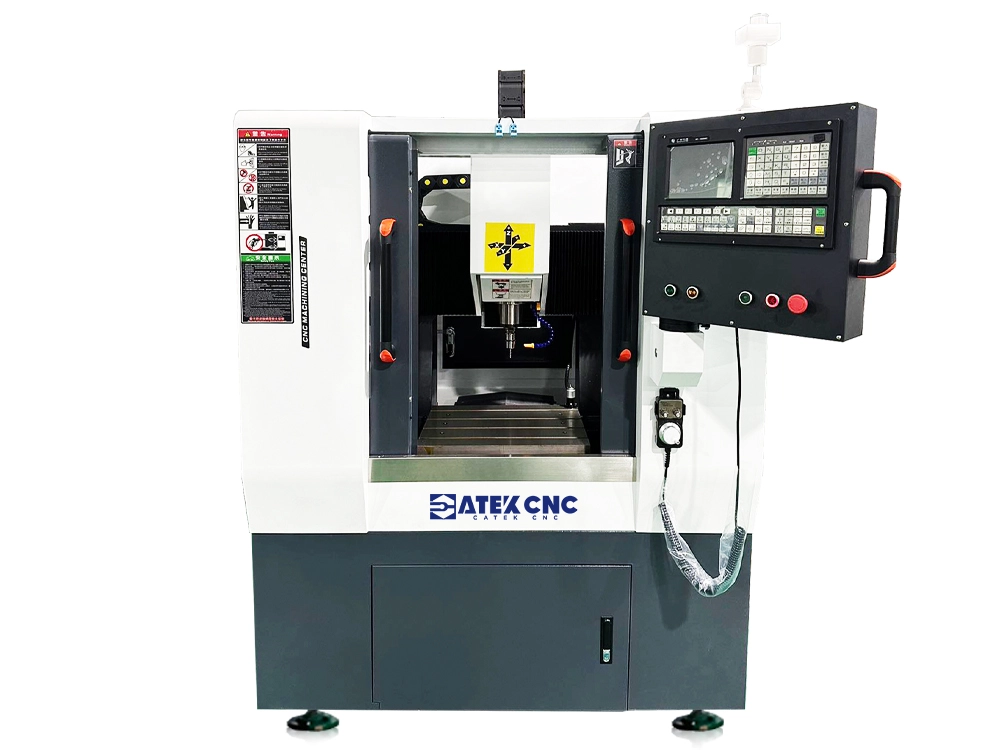
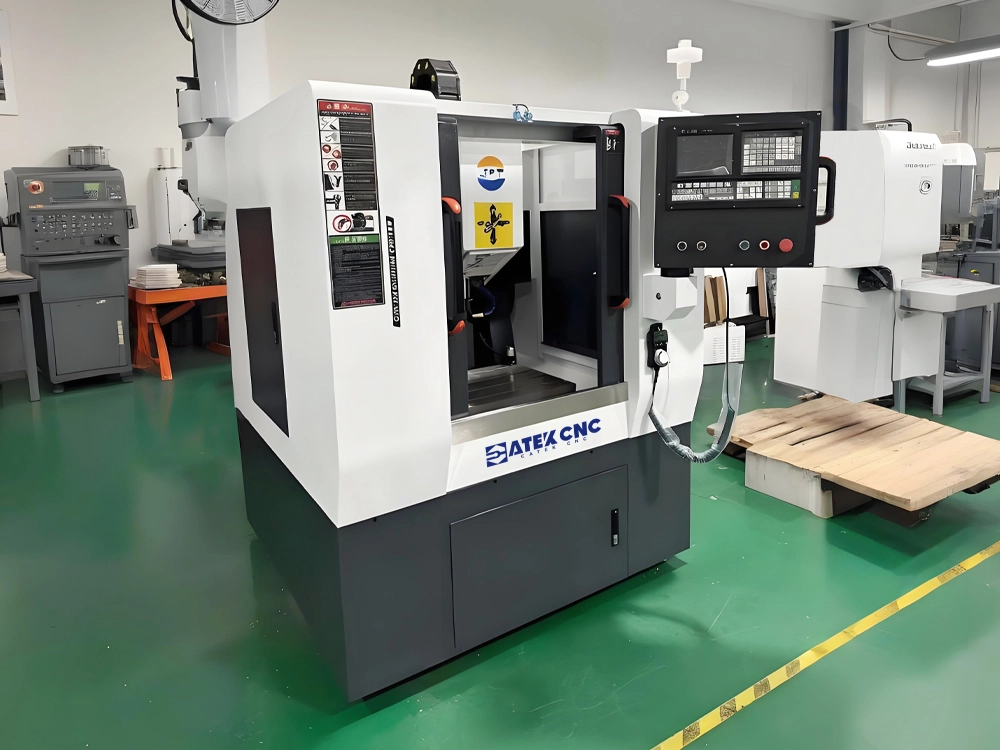
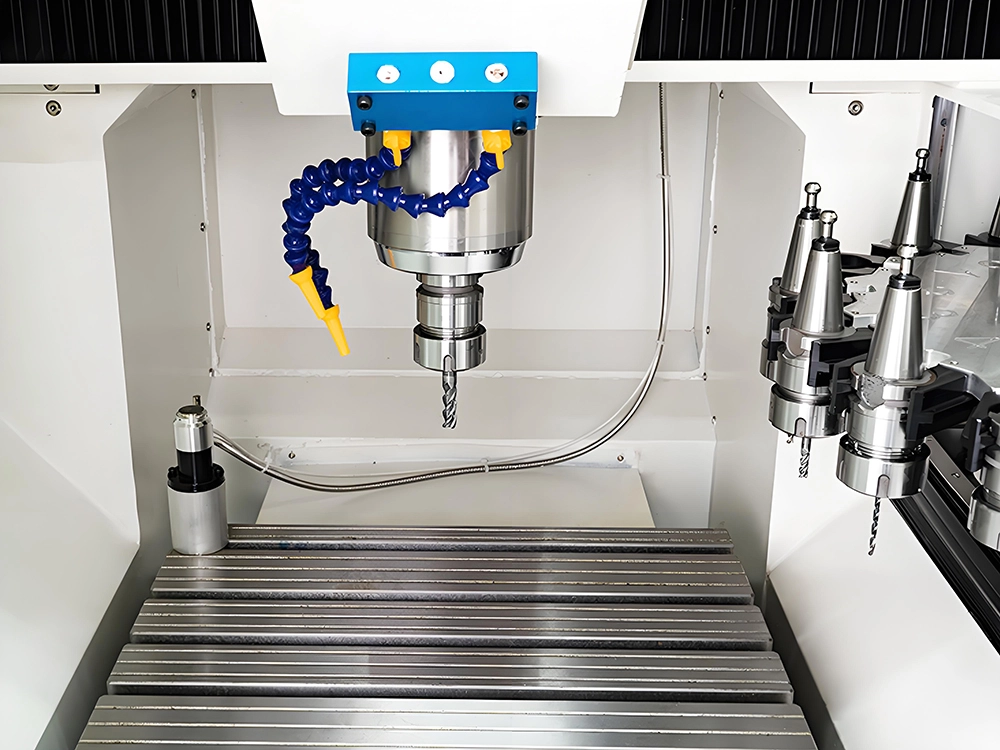

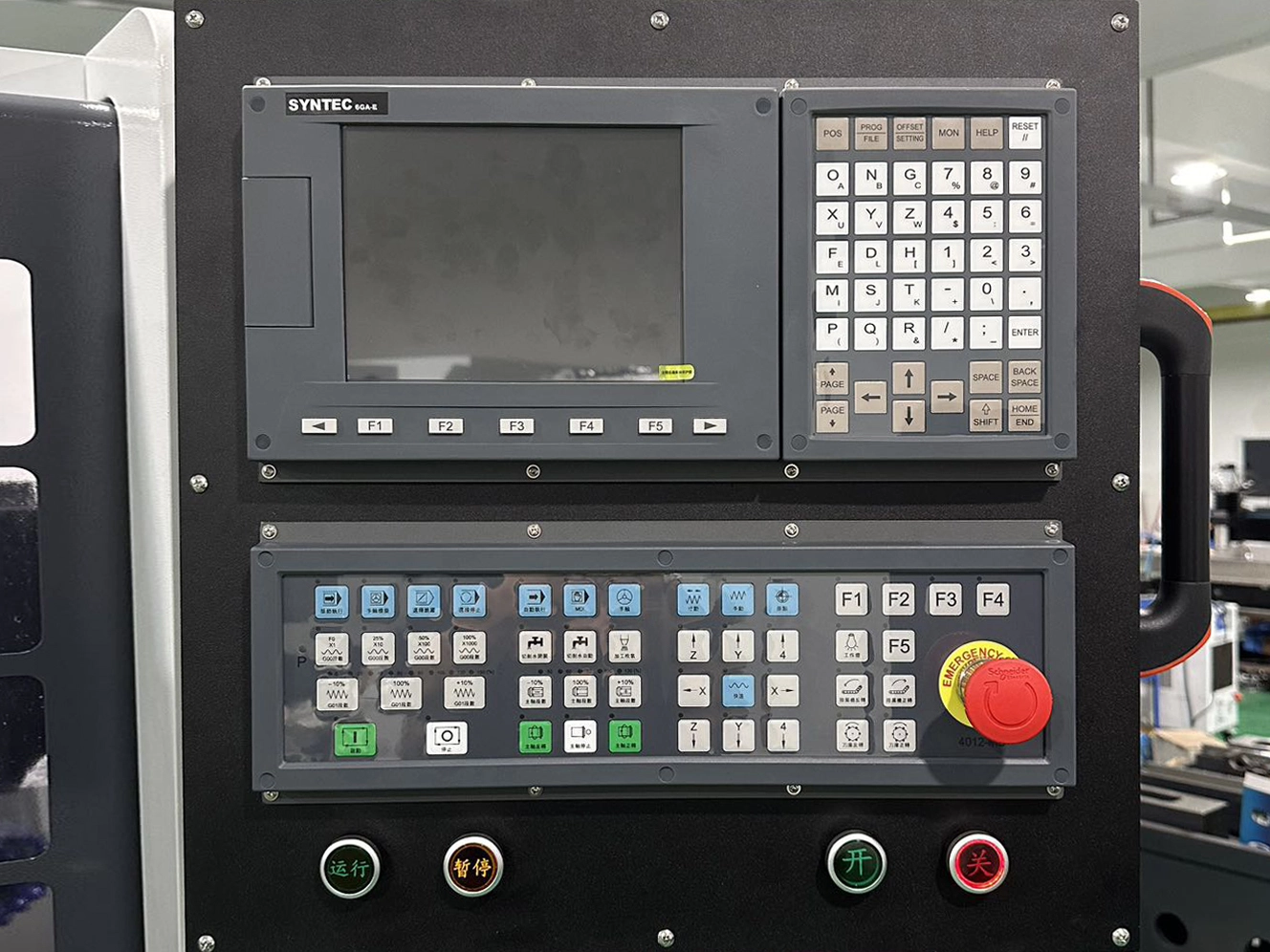
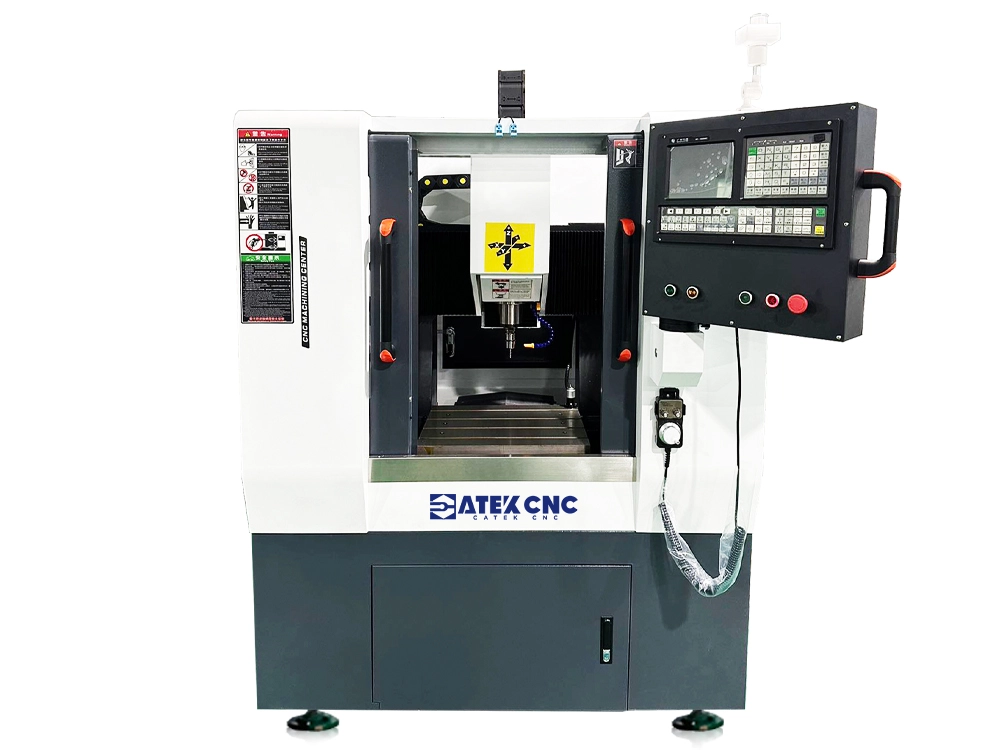
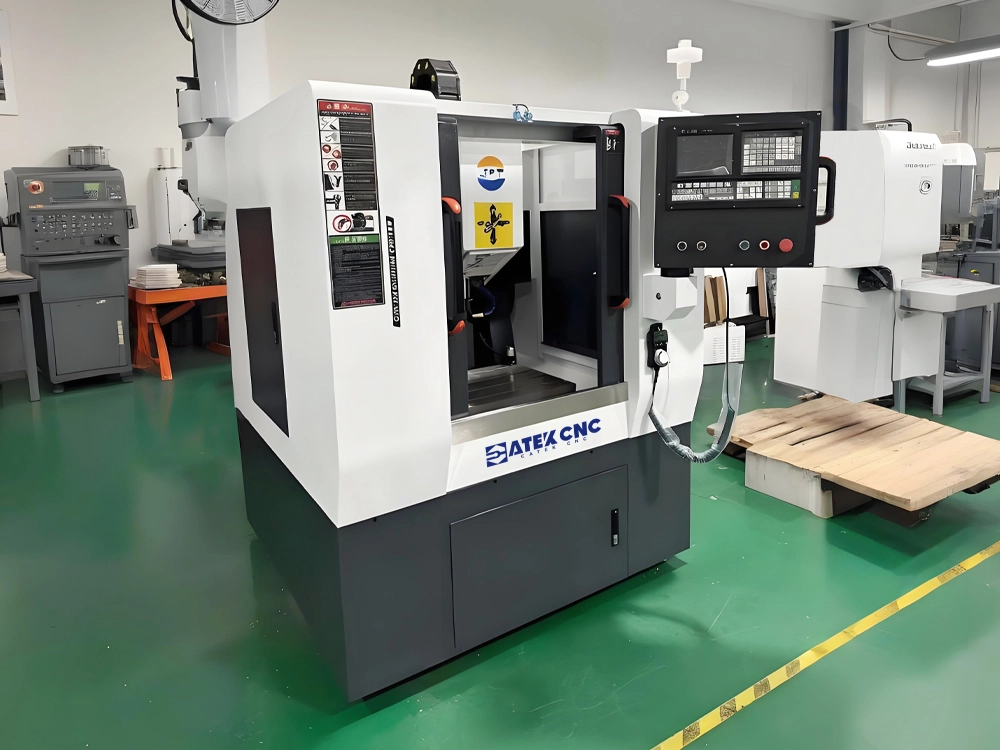
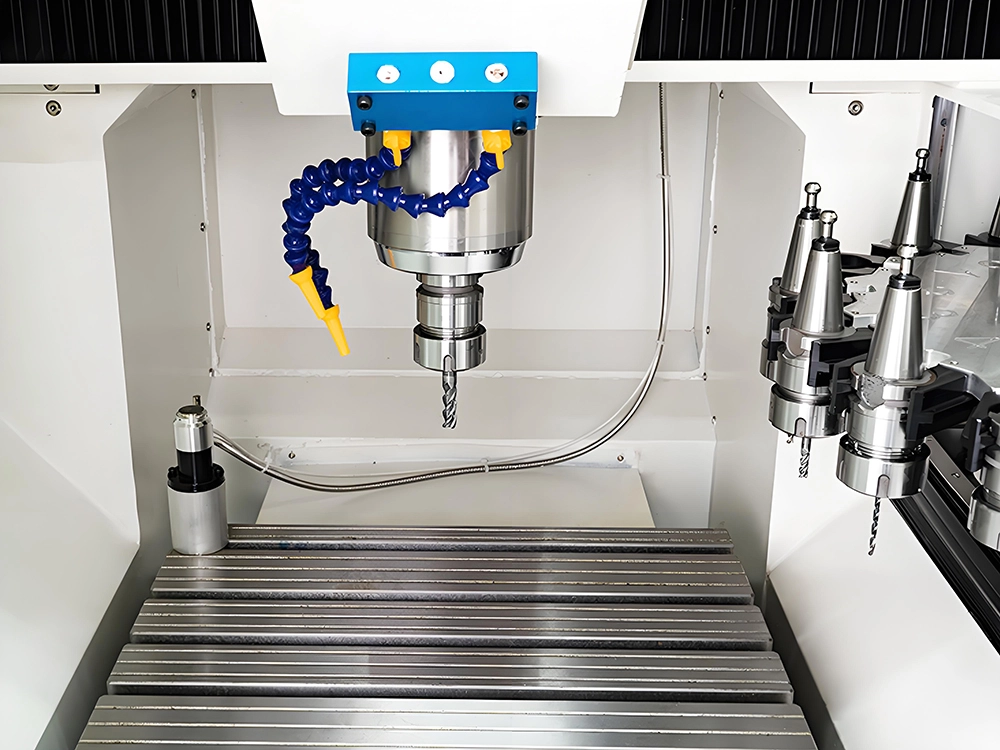

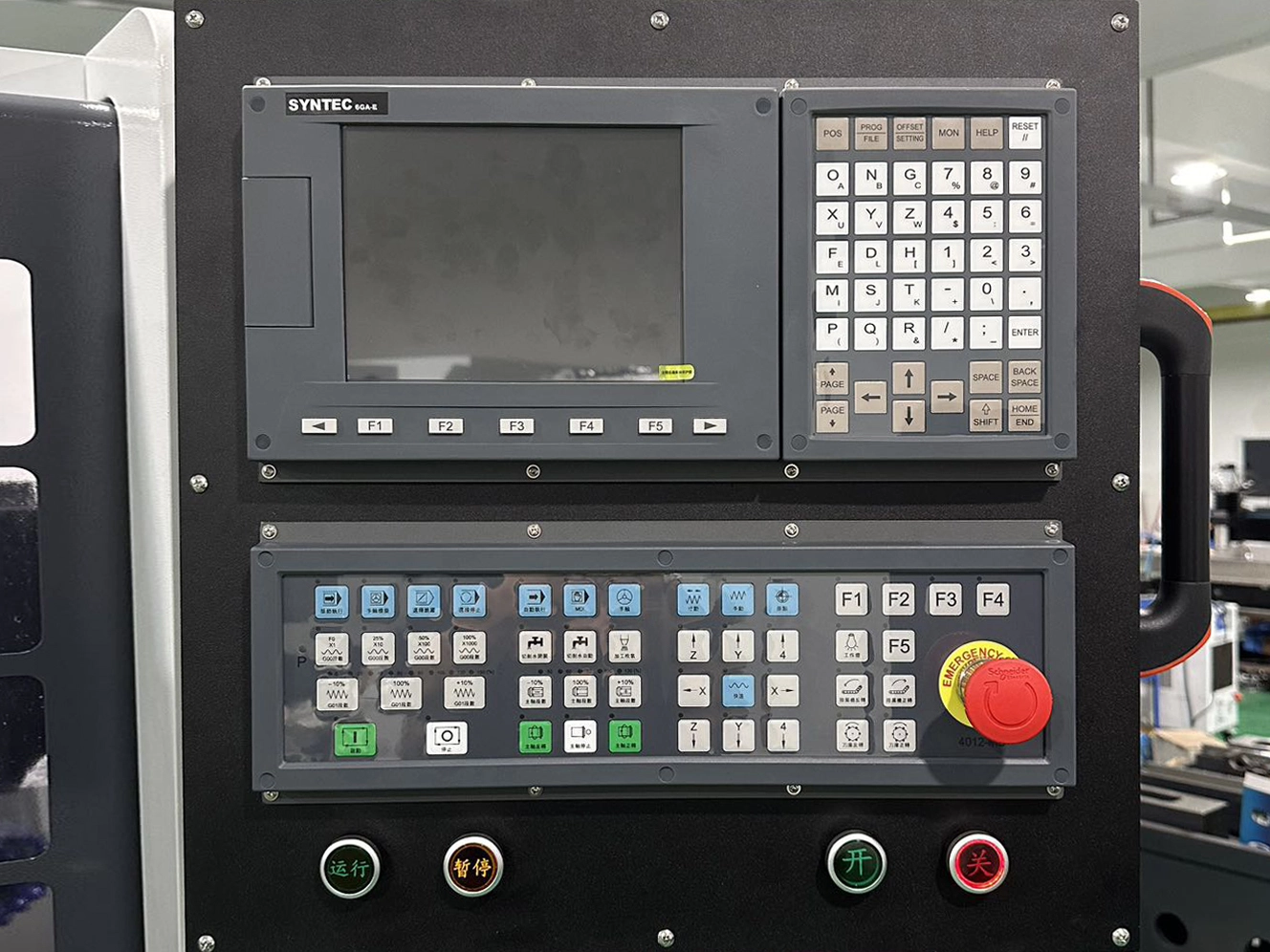
High Precision CNC ATC Metal Milling Machine
[Function Description]
CNC metal milling machines are a type of numerical control machinery specialized for use in the metal processing field. Their main function is to control the relative movement between the cutting tool and the workpiece through a numerical control system to complete various complex part processing tasks. CNC milling machines can perform operations such as planar milling, curved surface milling, engraving, drilling, and cutting on metal materials. They control the movement of the cutting tool by running G - code instructions in the control system to achieve precise processing of the workpiece. It can achieve very high processing accuracy. The accuracy of ordinary models can be controlled within 0.05 mm, and that of relatively high - end models can reach within 0.01 mm. It can process parts with complex shapes and strict dimensional accuracy requirements, such as molds, aerospace components, automotive components, medical device components, etc. CNC metal milling machines are characterized by high precision, high efficiency, versatility, and flexibility. They greatly reduce the labor intensity of workers, improve production efficiency and product quality, and at the same time reduce production costs and operation risks. They are widely favored in many countries including the United States, Canada, Brazil, United Kingdom, and EU.
Working Principle of a CNC Metal Milling Machine
A CNC metal milling machine utilizes CNC technology to control the movement of the machine's axes through computer programs, achieving high-precision and high-efficiency metal processing.
Input g-code instruction:
Based on the technical requirements of the part (such as shape, dimensions, machining methods, etc.), the G-code machining program is either manually written through the CNC system or automatically generated using CAD/CAM software based on the design drawings. These instructions include tool parameters, part parameters, cutting speed, feed rate, XYZ axis motion trajectory, and other information.
CNC system operation and processing:
After receiving the machining instructions, the CNC system performs internal calculations and processing, converting the complex machining trajectory into motion commands for the machine's moving components.
Servo drive and motion control:
The CNC system sends the processed commands to the machine's servo motors, which drive the various components to move the tool and workpiece along the preset trajectory. Through three-dimensional positioning in the X, Y, and Z directions, the part is machined as required.
Features of CNC Metal Milling Machine with Automatic Tool Changer
- The machine bed is made of high-strength cast iron and undergoes secondary annealing treatment, ensuring high rigidity and stability. It resists deformation even during prolonged use.
- Equipped with an automatic tool changer, it significantly reduces time wasted on manual tool changes, improves production efficiency, and greatly enhances machine utilization.
- A fully enclosed protective cover design effectively prevents splashes of cutting fluid and metal chips from harming workers, while also avoiding tool damage and equipment malfunctions, ensuring operator safety.
- Includes various auxiliary automation functions, such as an automatic lubrication system and an automatic cooling system, effectively improving production efficiency and operational convenience.
- Utilizes German-made ball screws, linear guides, and precision bearings, enhancing the machine's dynamic accuracy and load capacity for smoother operation.
- Compact vertical design with a small footprint, allowing one operator to manage multiple machines conveniently.
Advantages of CNC ATC Metal Milling Machine
- One-piece cast bed ensures stable accuracy and excellent wear resistance.
- High-precision ground ball screws with accuracy up to 0.01mm.
- Automatic tool-changing BT30 electric spindle, compatible with linear or rotary tool magazines.
- High-precision automatic tool setter, waterproof and dustproof, with a tool setting accuracy of 0.001mm.
- Double-layer filtration system in the base effectively filters waste residues and prevents clogging of coolant pipes.
- Taiwan Syntec CNC control system, featuring comprehensive functions and user-friendly operation.
- Japanese Yaskawa servo motors, offering high positioning accuracy and low noise.
- One-piece cast steel T-slot worktable, precision-ground multiple times for enhanced durability.
- Automatic oil lubrication pump for timed lubrication and maintenance of the entire machine.
- Fully enclosed protective cover effectively reduces noise pollution and improves the working environment by soundproofing.
Details of CNC ATC Metal Milling Machine
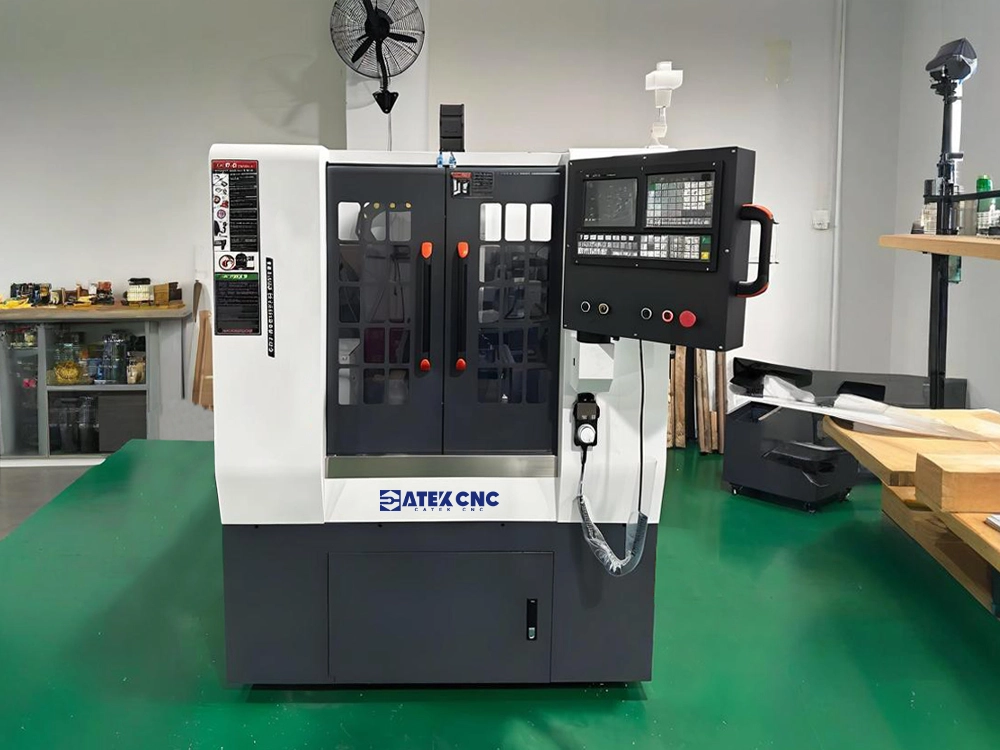

- Machine frame
The base is cast as a single piece, ensuring stable accuracy and excellent wear resistance. The column is 120mm thick, providing high strength, greater load capacity, and superior stability.
- Automatic tool change spindle
BT30 spindle, compatible with linear or rotary tool magazines. Equipped with a cutting fluid cooling system to cool the tool and workpiece and flush away metal chips.
- Workbench
Cast iron workbench, undergoes two rounds of manual annealing treatment. The installation platform is processed using a five-face gantry milling industrial machine, offering higher precision and greater durability.
- Carousel tool changer
Can hold up to 16 tools at once, covering a variety of machining tools, allowing even complex parts to be completed in one go.
- Linear tool changer
Features fast tool changing and high precision.
- Automatic tool setting device
The tool tip position can be measured and fed back to the control system to make corresponding compensation.
- Optional rotary axis
There are two types of devices that can clamp and rotate the workpiece to machine multiple faces or angles.
- Transmission system
Ground ball screw, high-precision guide rail and rack, higher precision and stable operation.
- Control system
You can choose control systems from Taiwan Syntec or Guangzhou Keyuan.
Technical Parameters of CNC ATC Metal Milling Machine
Model | CK-600D | CK-600 |
---|---|---|
Positioning Accuracy | 0.01mm | 0.01mm |
Repeat Positioning Accuracy | 0.008mm | 0.008mm |
X, Y Verticality | 0.015mm | 0.015mm |
Effective Stroke | 550×600×200mm | 550×600×200mm |
Worktable Size | 640×640mm | 640×640mm |
Working Height | 250mm | 250mm |
Rapid Speed | ≤ 10000mm/min | ≤ 10000mm/min |
Spindle Power | 5.5KW automatic tool change spindle | 4.5KW spindle |
Spindle Speed | 0-24000rpm (infinitely variable speed) | 0-24000rpm (infinitely variable speed) |
Tool Holder Specifications | BT30-ER25 | ER25/ER20 |
Tool Magazine | Linear tool magazine / carousel tool magazine | None |
Tool Magazine capacity | 6/16 | None |
Air Pressure | ≥ 0.8MPa | None |
Drive System | 750W servo motor | 750W servo motor |
Control System | Taiwan Syntec / Guangzhou Keyuan | Taiwan Syntec / Guangzhou Keyuan |
Guide Rail | Taiwan P grade | Taiwan P grade |
Screw | Taiwan ground screw | Taiwan ground screw |
Power Supply Voltage | AC380V | AC380V |
Material | HT250 aging treatment | HT250 aging treatment |
Weight | 1250kg | 1150kg |
Dimensions | 1300×1600×1980mm | 1300×1600×1980mm |
What Can CNC Metal Milling Machine Process?
A CNC metal milling machine with an automatic tool changer can perform engraving, cutting, milling, drilling, and other machining operations on a wide range of materials, including iron, steel, aluminum, copper, alloys, stainless steel, wood, plastics, and composite materials. It is widely used for processing molds, such as injection molds, stamping molds, and die-casting molds, as well as gears, sprockets, ratchets, spline shafts, automotive engine components, and body structural parts. It is also suitable for precision parts in electronics like mobile phones and computers (e.g., casings, panels, buttons), as well as sculptures, decorations, watches, watch components, electrodes, and copper electrodes.
Difference Between CNC Milling Machines With and Without Automatic Tool Changers
CNC metal milling machines with and without automatic tool changers differ significantly in terms of functionality, efficiency, and application scope:
- Functional Differences:
CNC Milling Machine with Automatic Tool Changer:
Equipped with an automatic tool changer, it can automatically switch tools, allowing a part to be clamped once and undergo multiple processes such as milling, drilling, and engraving. This eliminates the need for manual intervention, improving machining efficiency and precision.
CNC Milling Machine without Automatic Tool Changer:
Requires manual tool changes by operators, making it suitable for parts with fewer tool types or simpler machining processes. Frequent stops for manual tool changes reduce efficiency.
- Production Efficiency Differences:
CNC Metal Milling Machine with Automatic Tool Changer:
The automatic tool changer significantly reduces tool change time and downtime, enhancing production efficiency. Ideal for mass production and complex multi-process parts.
CNC Metal Milling Machine without Automatic Tool Changer:
Manual tool changes increase downtime, resulting in lower production efficiency. Suitable for small batches, single-variety, or simple machining tasks.
- Precision and Reliability:
CNC Metal Milling Machine with Automatic Tool Changer:
Ensures repeatable tool positioning accuracy, reducing errors caused by manual operations, and improving machining precision and product quality.
CNC Metal Milling Machine without Automatic Tool Changer:
Manual tool changes may lead to positioning errors due to improper handling, affecting machining accuracy and consistency.
- Cost:
CNC Metal Milling Machine with Automatic Tool Changer:
Higher initial cost due to the tool changer, tool magazine, and related components. However, its efficiency and reliability can reduce long-term production and labor costs.
CNC Metal Milling Machine without Automatic Tool Changer:
Lower equipment cost but requires more manual labor and has lower efficiency.
How to Maintain and Service a CNC ATC Metal Milling Machine?
To ensure long-term efficient operation, regular maintenance of the tool magazine, tool changer, and mechanical structure is essential.
- Tool and Tool Magazine Cleaning: Regularly inspect and clean tools and the tool magazine to prevent chips and debris from affecting tool clamping or positioning accuracy.
- Tool Clamping Reliability: Ensure tools are securely locked in place during manual installation.
- Mechanical Structure Inspection: Check the tool changer's mechanical components for proper operation and wear, replacing parts as necessary.
- Lubrication System Maintenance: Regularly inspect the lubrication system and oil pump, adding lubricant to ensure smooth operation and reduce wear.
- Software Updates and Troubleshooting: Update the CNC system software to ensure stable operation of the tool change program.
- Dry Run Check: Before machining, simulate the process using drawings to ensure all components function properly, paying special attention to the smooth operation of the tool changer and robotic arm, and checking for collision risks during axis movements.
Model | CK-600D | CK-600 |
---|---|---|
Positioning Accuracy | 0.01mm | 0.01mm |
Repeat Positioning Accuracy | 0.008mm | 0.008mm |
X, Y Verticality | 0.015mm | 0.015mm |
Effective Stroke | 550×600×200mm | 550×600×200mm |
Worktable Size | 640×640mm | 640×640mm |
Working Height | 250mm | 250mm |
Rapid Speed | ≤ 10000mm/min | ≤ 10000mm/min |
Spindle Power | 5.5KW automatic tool change spindle | 4.5KW spindle |
Spindle Speed | 0-24000rpm (infinitely variable speed) | 0-24000rpm (infinitely variable speed) |
Tool Holder Specifications | BT30-ER25 | ER25/ER20 |
Tool Magazine | Linear tool magazine / carousel tool magazine | None |
Tool Magazine capacity | 6/16 | None |
Air Pressure | ≥ 0.8MPa | None |
Drive System | 750W servo motor | 750W servo motor |
Control System | Taiwan Syntec / GuangZhou Keyuan | Taiwan Syntec / GuangZhou Keyuan |
Guide Rail | Taiwan P grade | Taiwan P grade |
Screw | Taiwan ground screw | Taiwan ground screw |
Power Supply Voltage | AC380V | AC380V |
Material | HT250 aging treatment | HT250 aging treatment |
Weight | 1250kg | 1150kg |
Dimensions | 1300×1600×1980mm | 1300×1600×1980mm |
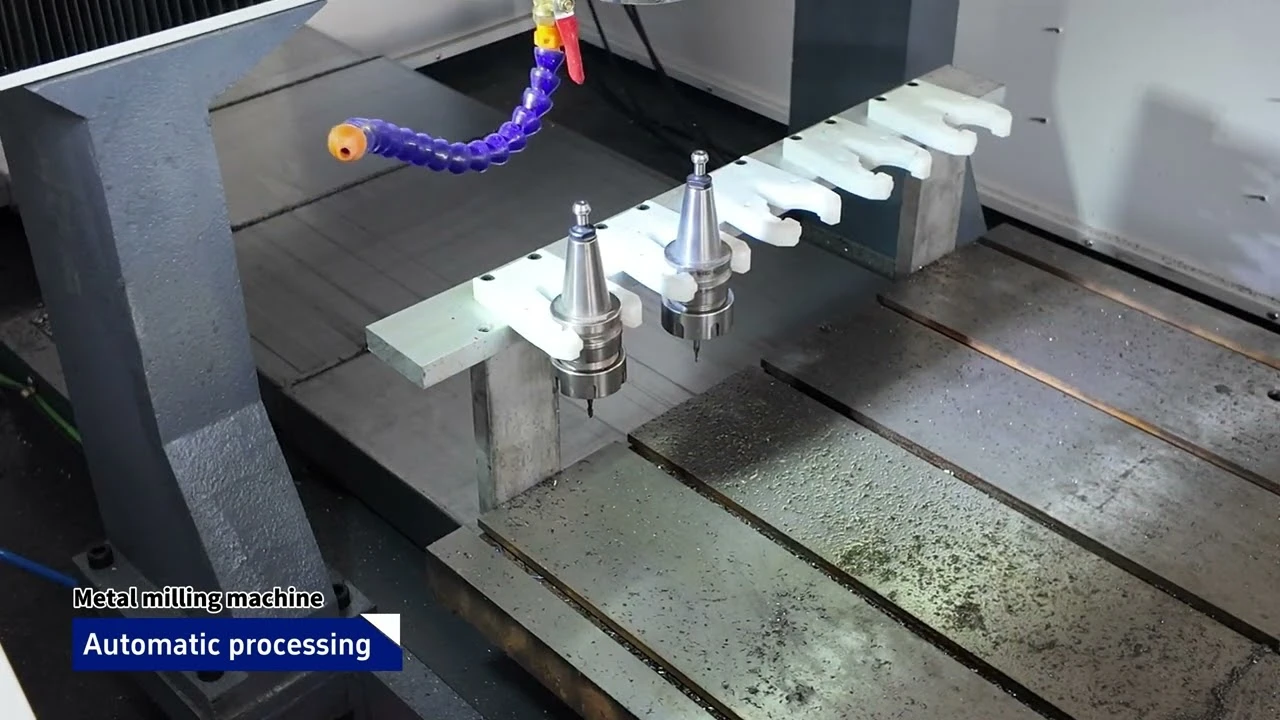
YOU MAY ALSO LIKE
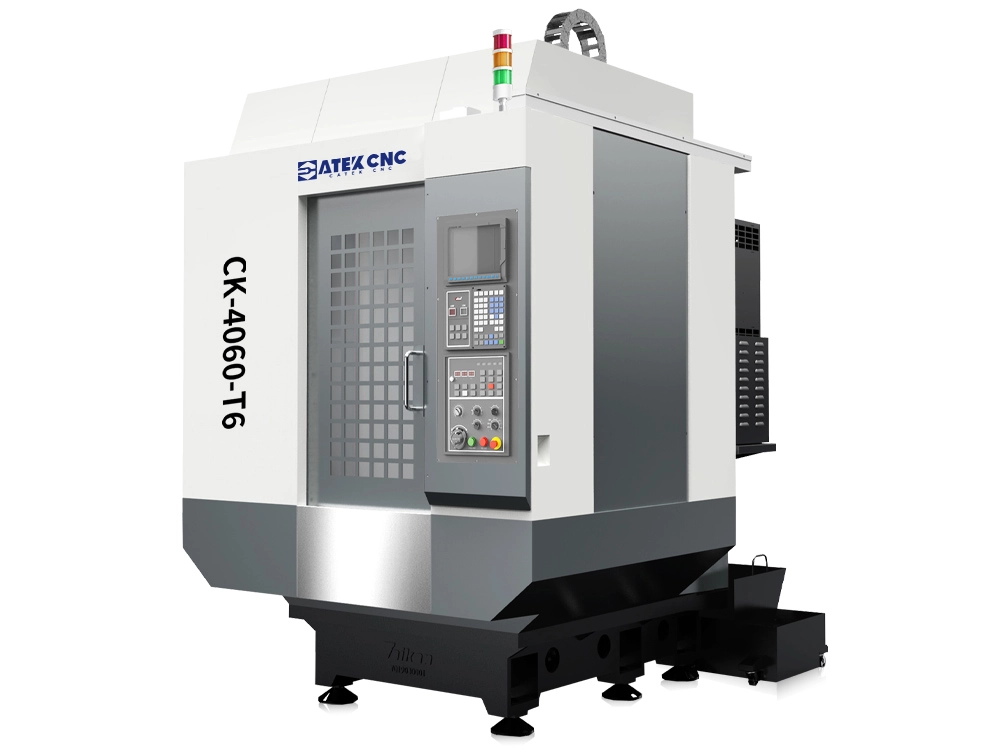
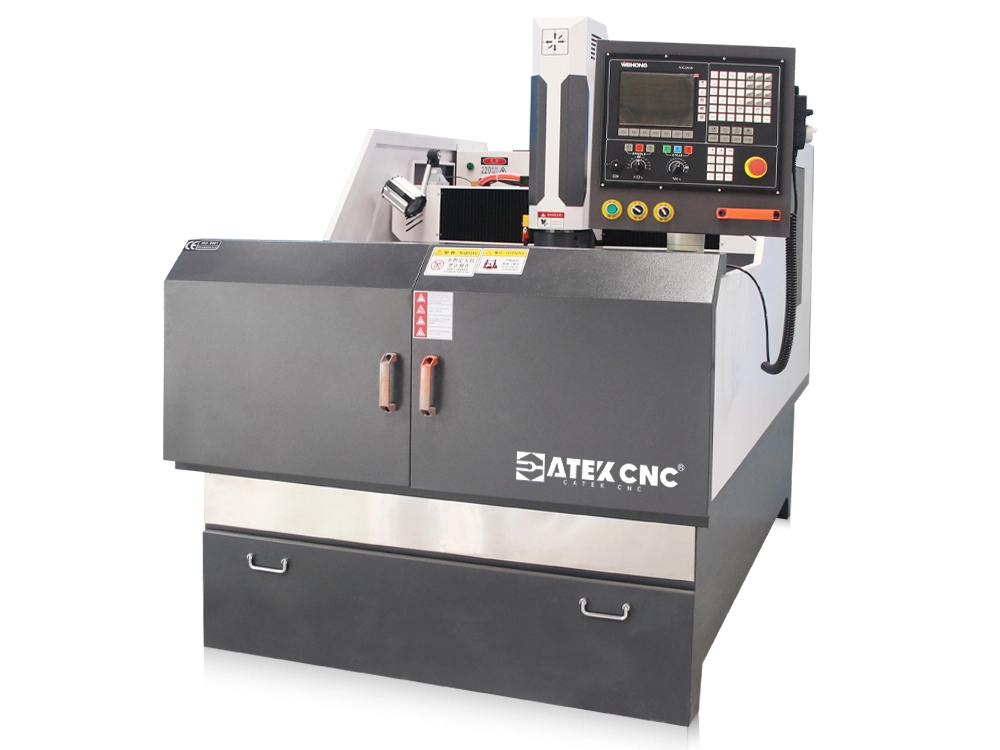
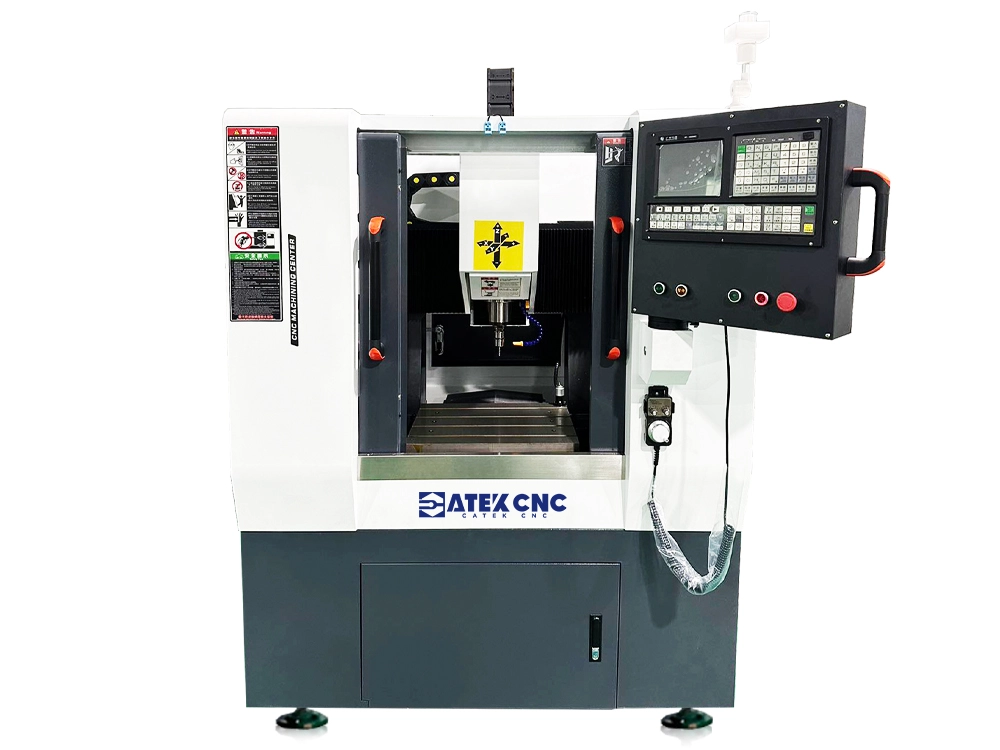
REVIEWS
Let more people know what you share.