Industrial High-Precision Metal Engraving, Cutting and Milling Machine
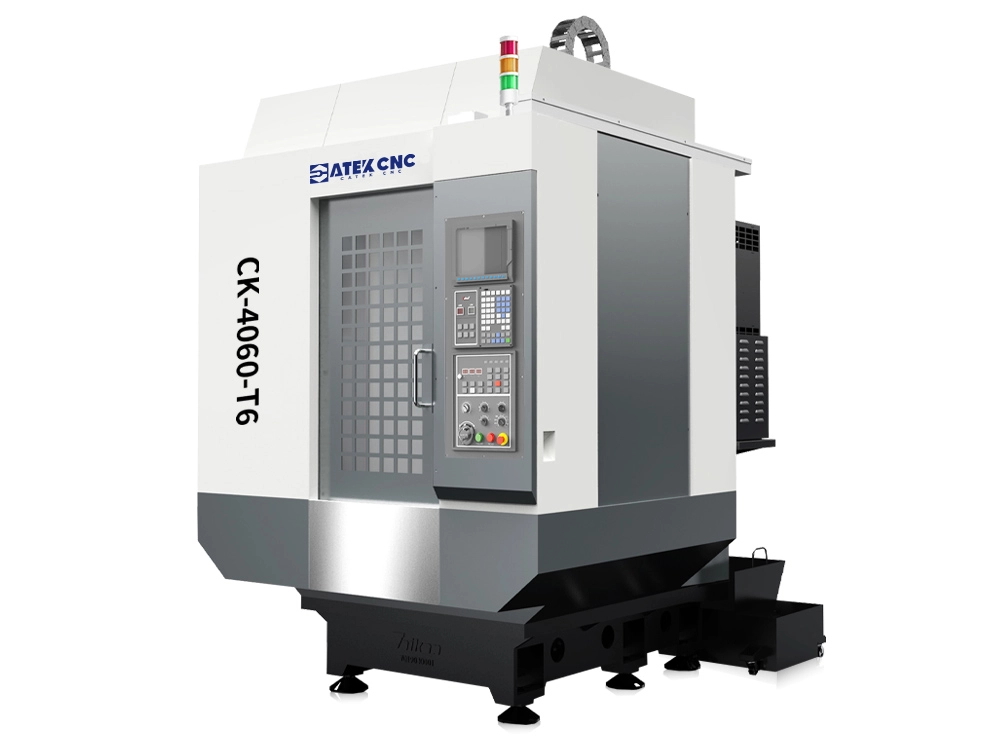
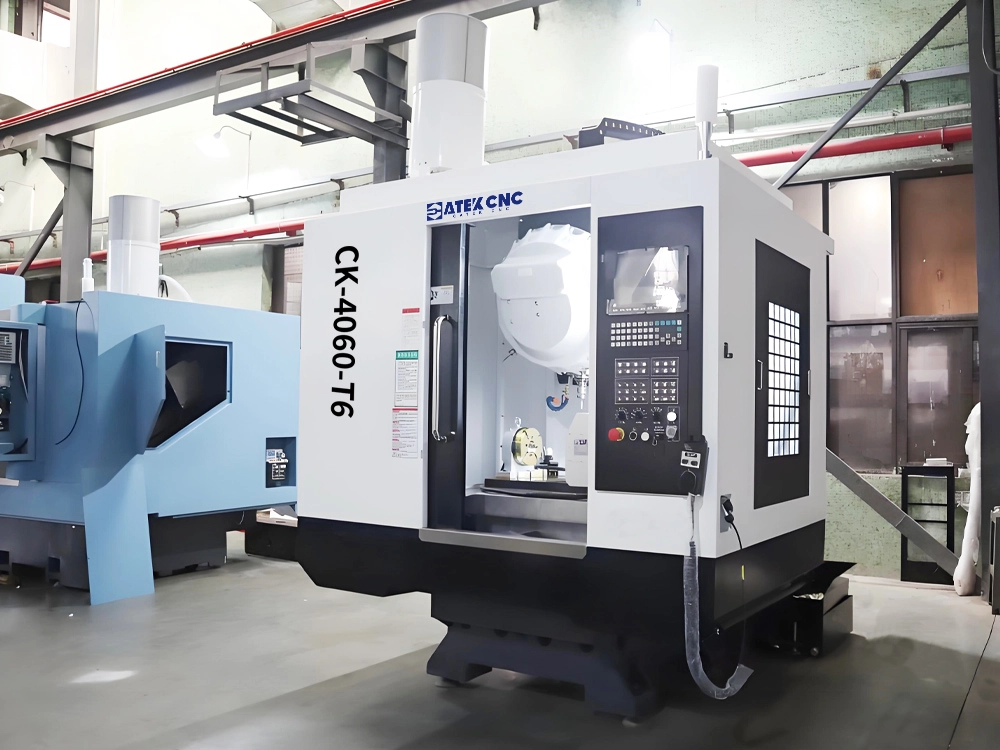
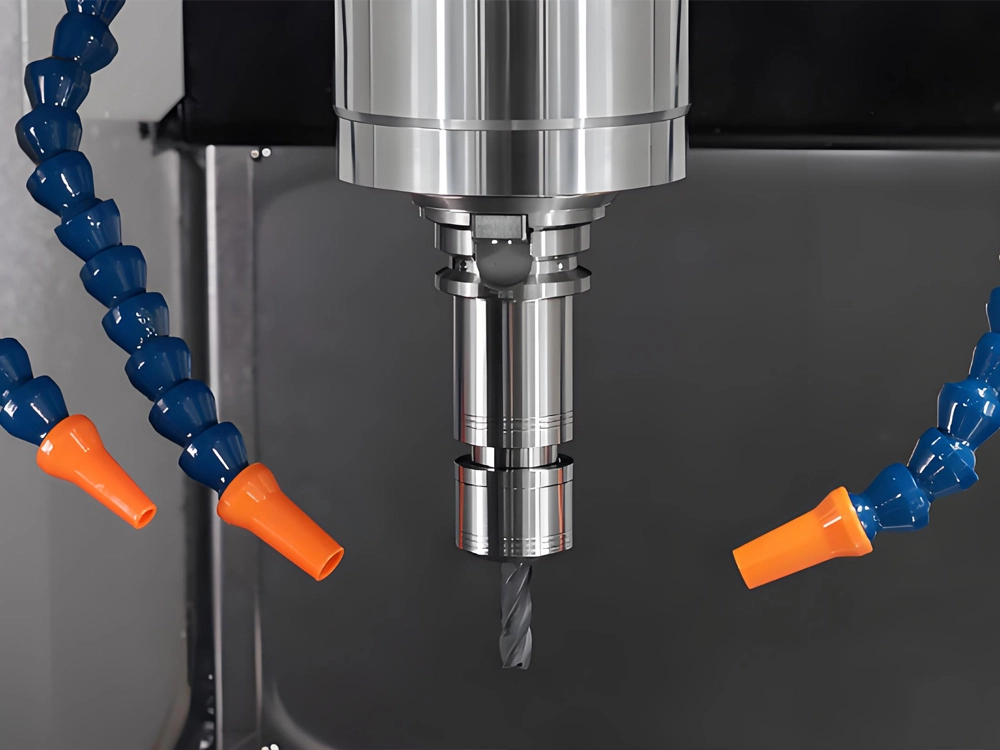
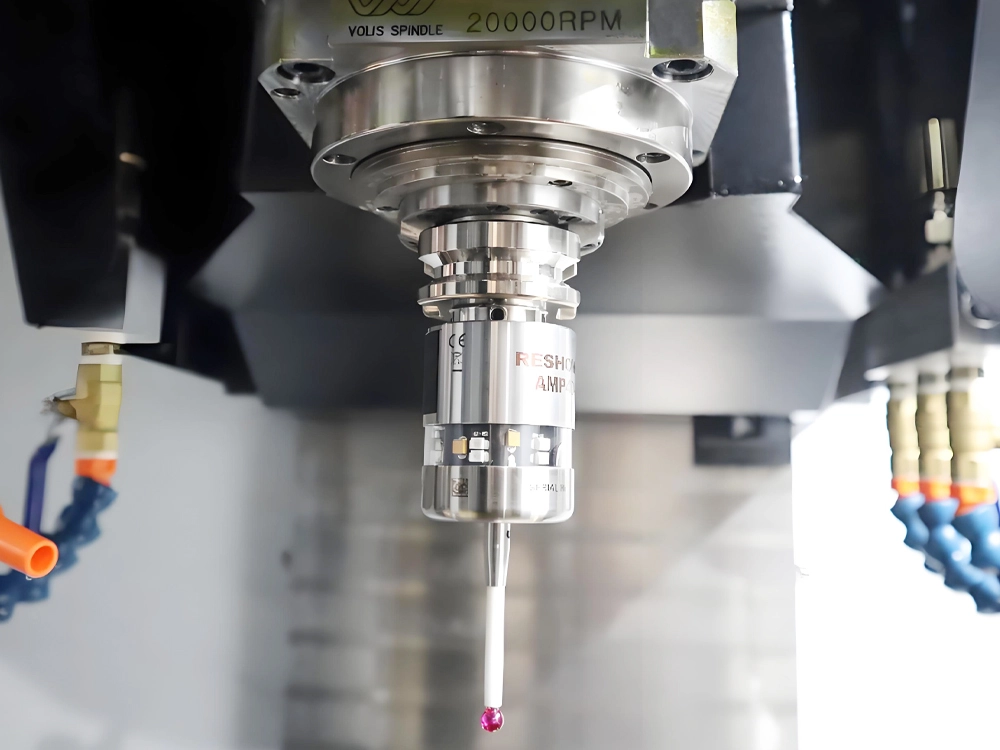
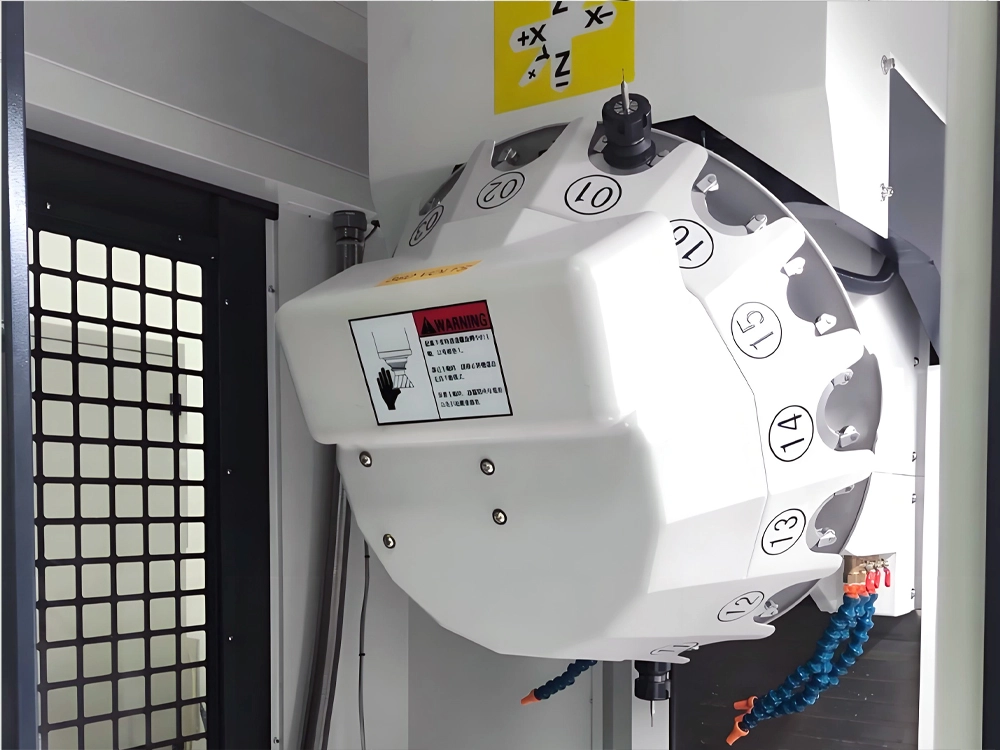
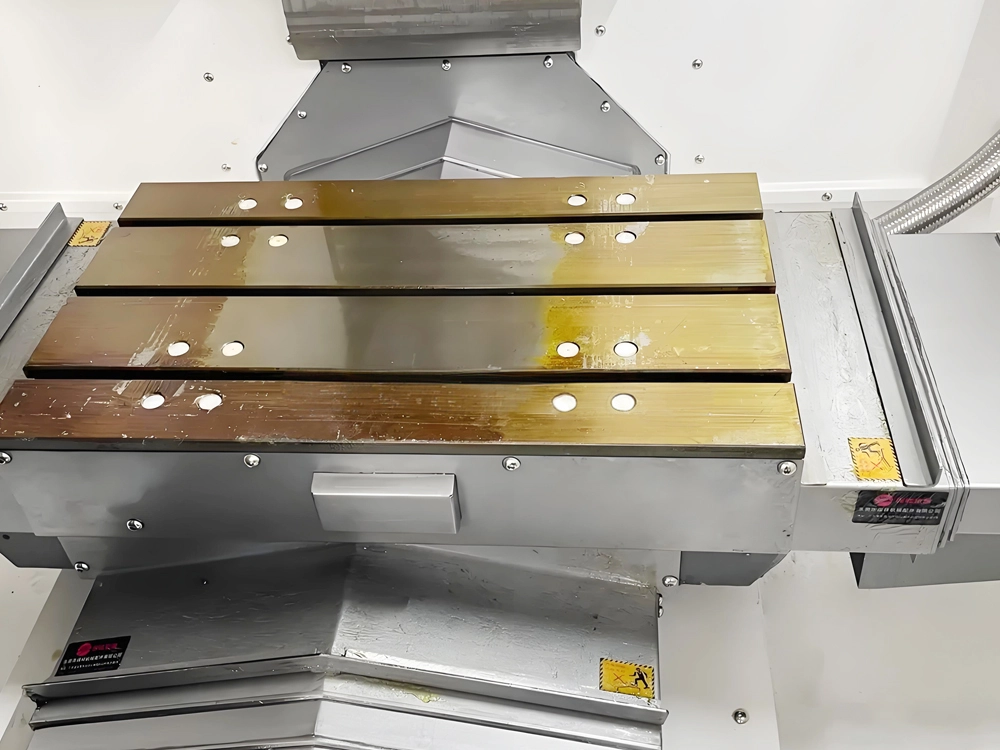
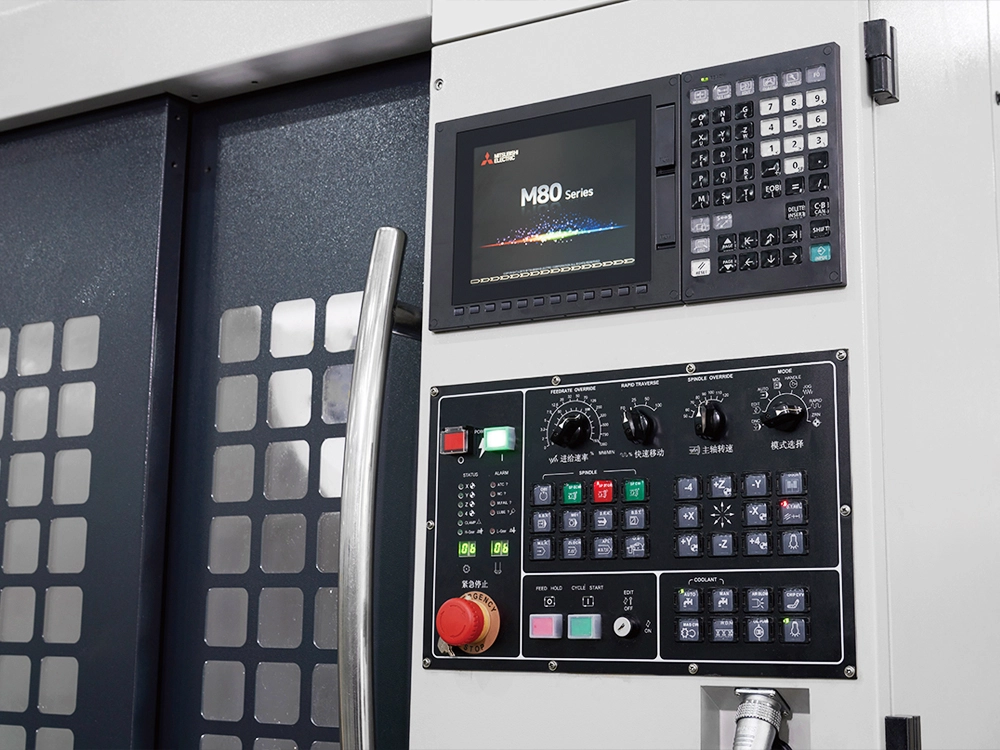
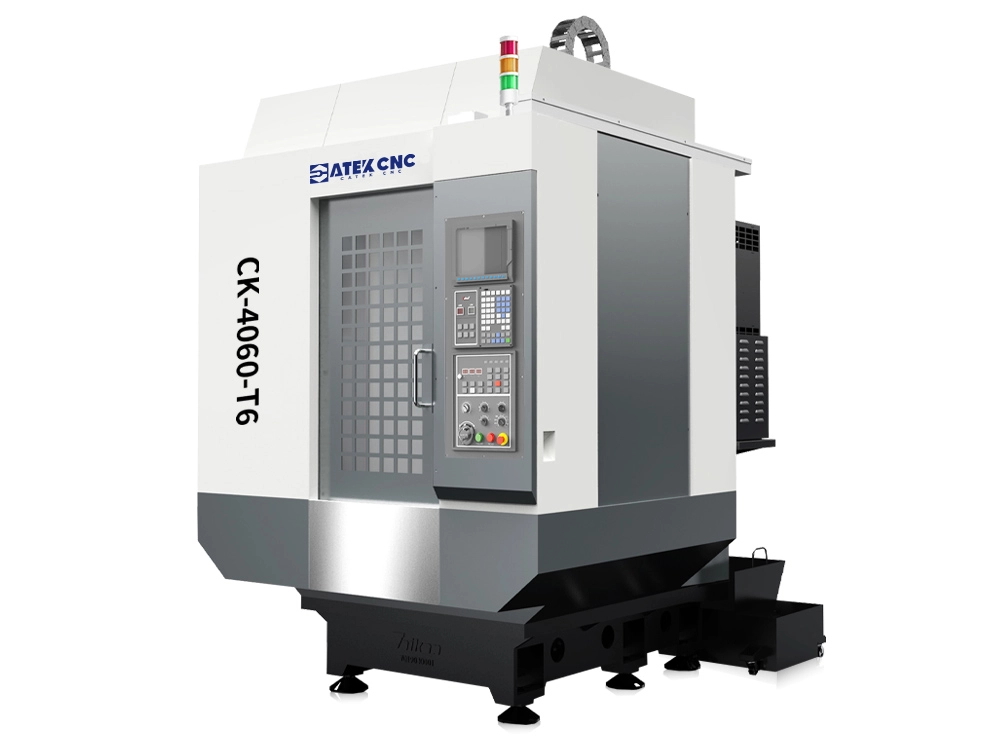
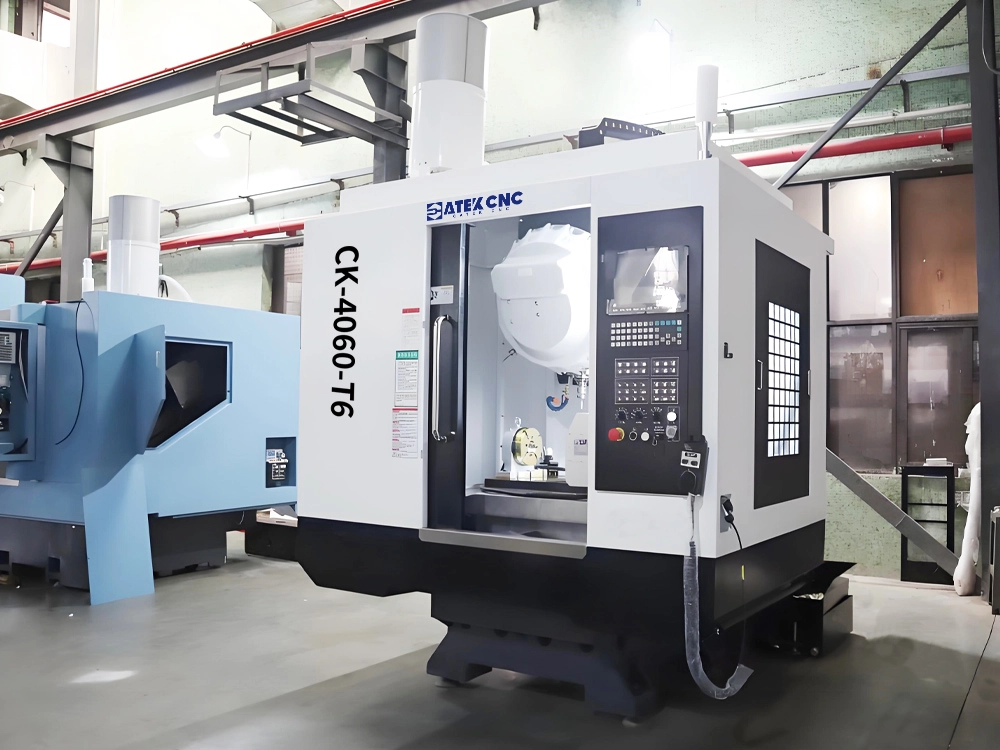
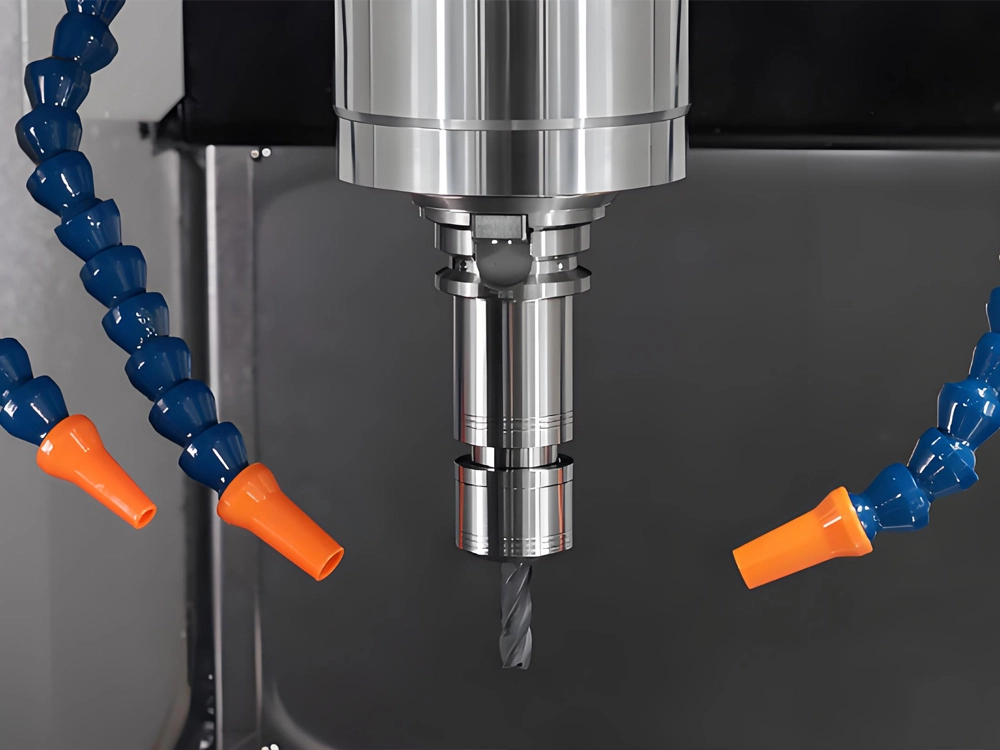
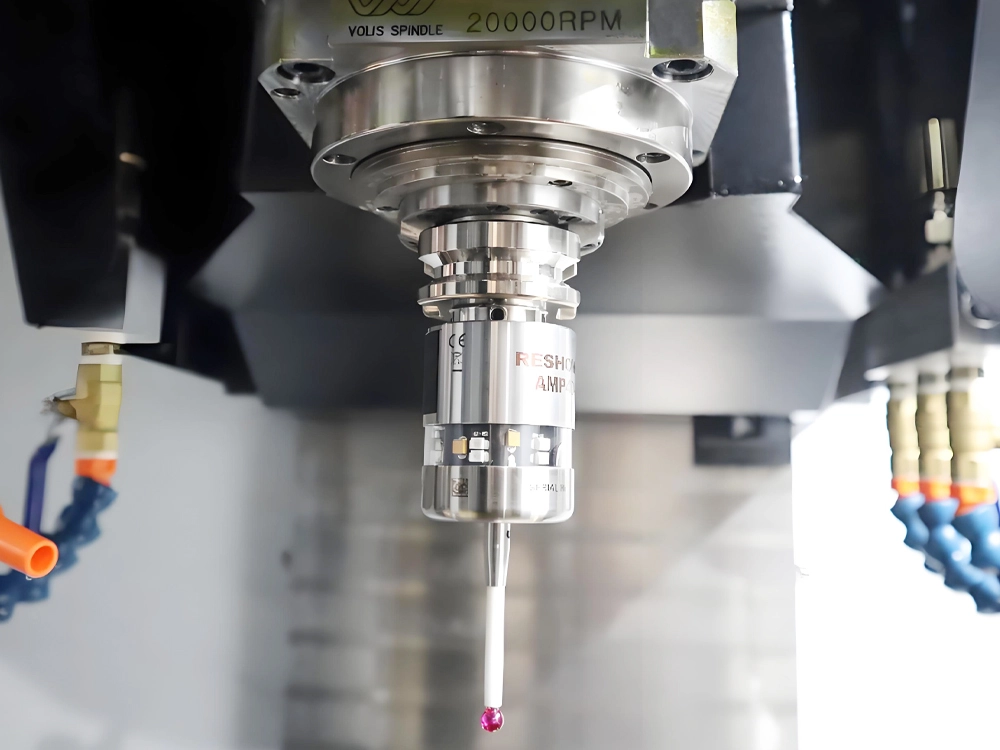
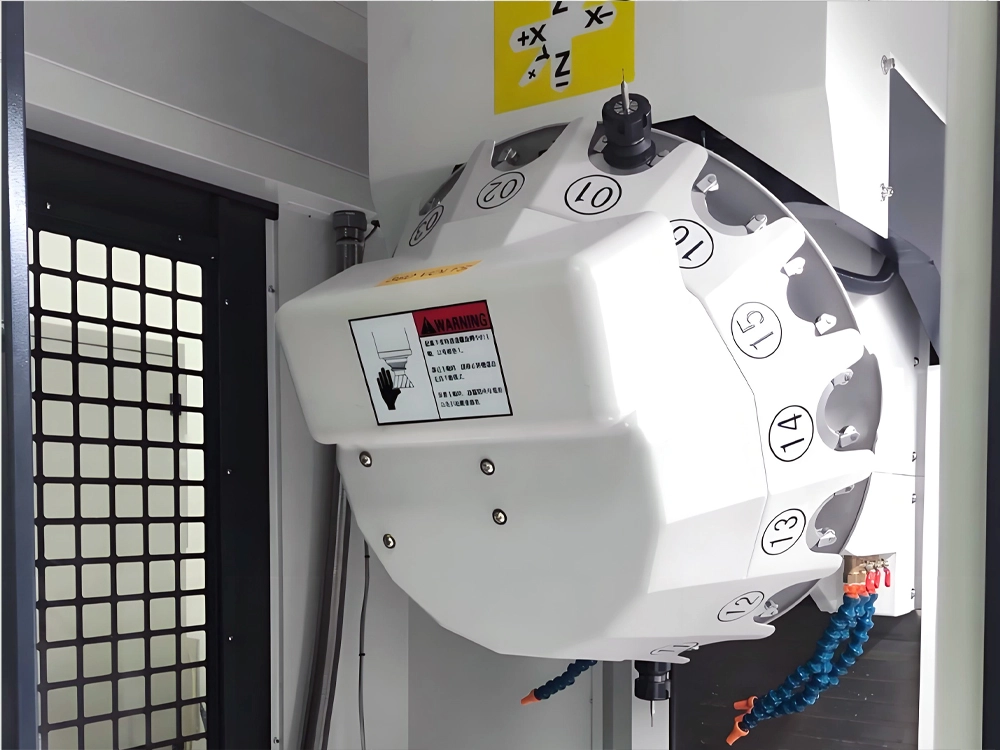
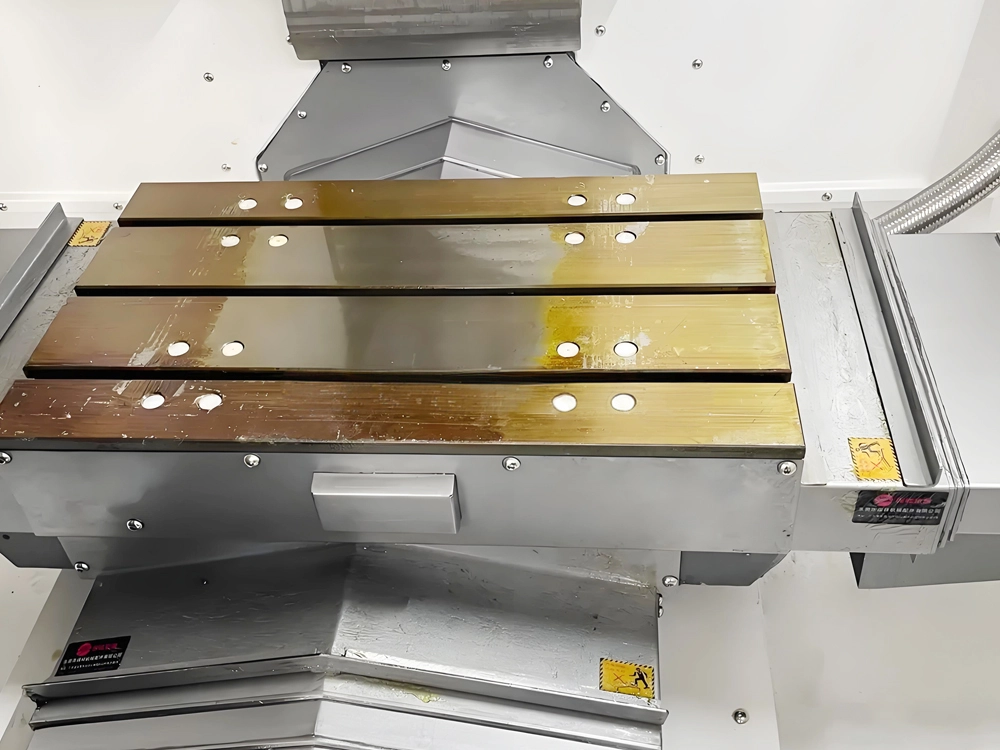
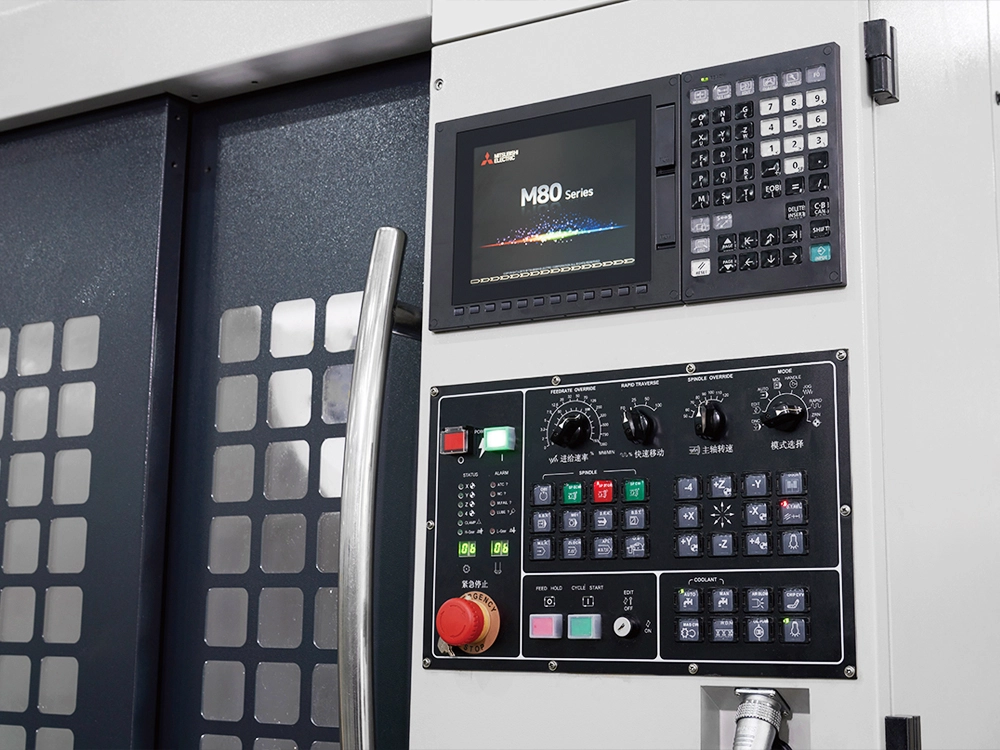
Metal Drilling and Milling Vertical Machining Centers for Sale
[Function Description]
The metal drilling and milling multifunctional vertical machining center is a CNC machine tool that integrates a variety of complex machining processes such as milling, drilling, tapping, reaming, boring, and thread cutting. It is equipped with a clamp-arm servo tool magazine that can install 8/16/21 tools at a time, and supports multi-axis rotation and linkage processing. It can adapt to various complex processing tasks and flexibly respond to various processing needs. Moreover, the equipment has a compact structure and a small footprint. It can be easily placed in both small workshops and large factories, and is suitable for use in a variety of environments.
This metal drilling and tapping vertical machining center designed by CATEKCNC uses a fully enclosed protective cover to provide all-round protection for the entire machine, effectively avoiding debris splashing and accidental collisions during processing, and ensuring the safety of operators. It is also equipped with a power-off protection switch to cope with various emergency situations. The control system can be selected from brands such as SYNTEC, Fanuc, and Siemens. The operation interface is simple and intuitive, and it is very friendly to beginners. It is worth mentioning that this vertical machining center not only has high performance and a wide range of processing, but it is also cheap and has a super high return on investment. If you are preparing to start a business or plan to expand the scale of production, you can learn more about this machine tool.
What Is a Metal Drilling and Milling Vertical Machining Center?
The metal metal drilling and milling vertical machining center is a highly automated, fully functional CNC machine tool with a spindle axis perpendicular to the workbench. It is mainly used to process metal parts and can efficiently complete multi-process processing tasks of complex parts. It integrates multiple processing functions and is controlled by a dedicated CNC system to minimize the useless time during processing. With a clamp-arm servo tool magazine, it can be equipped with 8/16/21 tools at a time, greatly reducing the clamping and replacement time of the workpiece during processing. At the same time, it has high-speed cutting processing capabilities, further improving production efficiency.
Advantages of Metal Drilling and Milling Vertical Machining Center
- Using an improved fuselage base, all structural components are analyzed and optimized using the finite element analysis method (FEA), and the casting process is used in appropriate locations to design and manufacture the strongest rigidity and stability to ensure the best processing effect.
- The three axes of XYZ all use an integrated bearing seat. All kinds of loads acting on the machine tool will eventually be transmitted to the bed through various links, which greatly improves the dynamic performance and transmission performance of the machine. The use of a low-center-of-gravity base has excellent stability and processing accuracy, which greatly reduces the vibration generated during processing.
- The use of a clamp-arm tool magazine that can accommodate 8/16/21 tools effectively increases the range of tool selection for machining. By optimizing the tool magazine structure and coordinating with the Z-axis movement of the milling machine, it is possible to quickly exchange long-distance tools and significantly shorten tool change time.
- Use constant power, high speed, high torque spindle (direct-connected spindle and belt-type spindle are optional), the maximum speed can reach 12000rpm, the processing is stable and efficient, the cutting finish is high, and it can meet various processing needs.
- The X-axis protective cover adopts a two-part fully movable design, which can achieve a larger moving stroke while occupying a smaller space, and remains stable even when moving quickly. The Y-axis protective cover uses a single-piece full-coverage protective cover, which is simple and reliable.
- The XY axis uses high-precision ball screws and high-precision linear guides. The use of HRV control technology improves dynamic performance. By optimizing the transmission ratio, the dynamic characteristics of the feed axis can be further enhanced, making the machine tool performance stronger.
- The touch probe can measure the workpiece and tool, monitor the machining process, and realize automatic calibration compensation to improve machining accuracy, efficiency and quality.
- The specially designed cooling and chip removal system allows the coolant to directly contact the tool and the surface of the machined part, while effectively removing waste chips to avoid scratching the workpiece surface.
- The spindle adopts air curtain protection technology, which can effectively prevent dust, water vapor and other impurities from entering the spindle bearings, protect the grease structure from being damaged, avoid performance degradation caused by the invasion of impurities, effectively extend the service life of the spindle, avoid tool jamming, tool drop, empty tool and other processing errors, and ensure precise synchronization during the operation of the spindle.
Details of Multifunctional CNC Metal Drilling, Tapping and Milling Machine
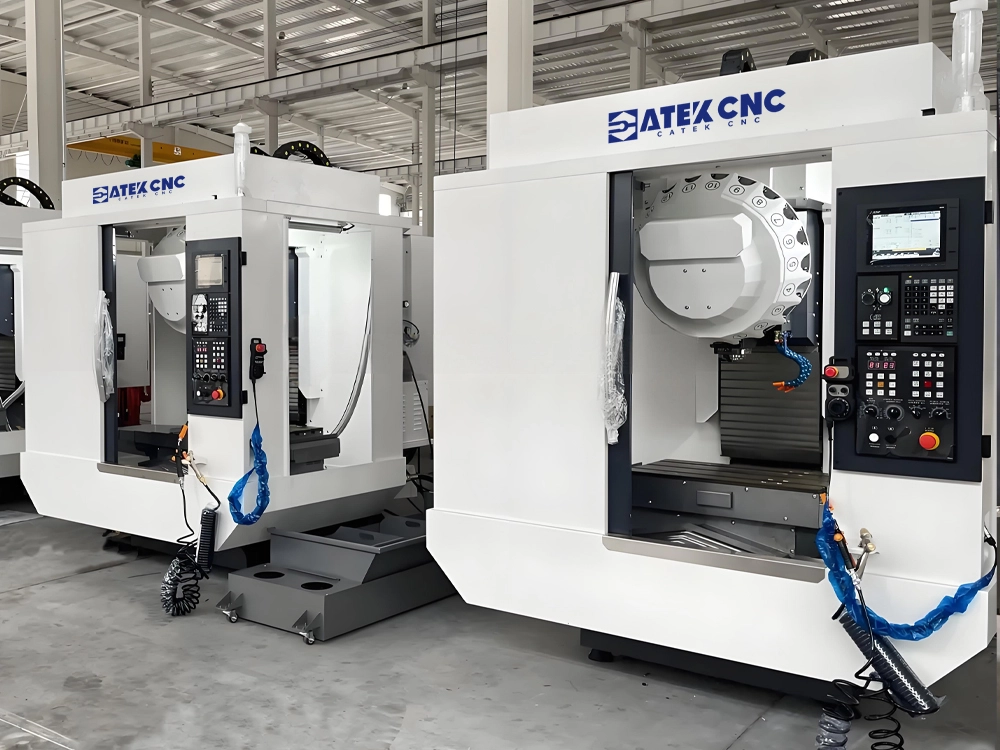
- Machine frame
The improved casting body has stronger stability and effectively reduces the vibration generated during processing.
- Direct-connected short-nose spindle
The direct-connected short-nose spindle offers significant advantages: it enhances rigidity, reduces vibration, and improves machining accuracy and surface quality; boosts cutting capability and optimizes power transmission; also improves heat dissipation conditions. Its compact structure helps increase machining flexibility while reducing space occupation and interference.
- Clamp-arm servo tool magazine
The clamp-arm servo tool magazine has a tool change speed of up to 1.4 seconds, operates at high speed and without noise, and the tool change process is faster and more accurate.
- Transmission system
Ground ball screws and high-precision sliders and rails, effectively reducing noise and vibration during mechanical operation and improving processing accuracy.
- Flood coolant system
There are three nozzles to spray coolant, each nozzle can be turned on and off independently.
- Movable workbench
The workbench can be moved along the X and Y axes and is covered with a T-slot table, which can flexibly clamp various workpieces.
- High-accuracy touch probes
This touch probe is designed to determine the exact coordinates of objects mounted on a CNC milling machine. The CNC system generates these coordinates when the touch probe stylus touches the object and uses them to link the processing program to the workpiece location, to measure lengths, diameters, to search for hole centers, etc.
- Control system
Optional Mitsubishi or Syntec control systems.
Mitsubishi system Syntec system - Improves machining accuracy and reduces single-piece processing time.
- Reduces gear backlash through position compensation.
- Automatically determines cutting conditions.
- High-speed synchronous tapping function.
- High-speed machining mode with high-precision control.
- High-efficiency machining performance.
- Rapid tap retraction and tool tip point control function.
- High-efficiency machining performance with handwheel simulation function.
- Optional indexing chuck
Used to clamp the workpiece and rotate it to process multiple faces or surfaces-of-revolution of the workpiece.
- CK-1050-T10
The larger workbench means it can process larger workpieces.
Technical Parameters of The Best Quality Metal Drilling and Tapping Vertical Machines
Model | CK-4060-T6 | CK-7045-T7 | CK-8050-T8 | CK-1050-T10 |
---|---|---|---|---|
X/Y/Z Axis Travel | 600/400/330mm | 700/450/330mm | 800/500/330mm | 1000/500/330mm |
Workbench Size (Length * Width) | 700*420mm | 800*420mm | 1000*500mm | 1100*500mm |
Processing Range | 600*400mm | 700*420mm | 800*500mm | 1000*500mm |
T-Slot (Center Distance * Slot Width * Number of Slots) | 3*14*125mm | 3*14*125mm | 5*18*100mm | 5*18*100mm |
Maximum Load of Workbench | 250kg | 250kg | 350kg | 350kg |
Spindle Nose to Work Table | 150-450mm | 150-450mm | 150-480mm | 150-480mm |
Spindle Center to Column Guide Surface | 460mm | 460mm | 540mm | 540mm |
Spindle Taper | BT30 | BT30 | BT30 | BT30 |
Spindle Speed | 12000/20000rpm | 12000/20000rpm | 12000/20000rpm | 12000/20000rpm |
Spindle Diameter | 105mm | 105mm | 105mm | 105mm |
Spindle Bearing | 4XNSK7010C | 4XNSK7010C | 4XNSK7010C | 4XNSK7010C |
Spindle Drive Mode | Direct Connected | Direct Connected | Direct Connected | Direct Connected |
Spindle Motor | 5.5-7.5kw | 5.5-7.5kw | 7.5kw | 7.5kw |
Cutting Feed (X/Y/Z Axis) | 12000/12000/12000mm/min | 12000/12000/12000mm/min | 12000/12000/12000mm/min | 12000/12000/12000mm/min |
Rapid Feed (X/Y/Z Axis) | 48/48/48m/min | 48/48/48m/min | 48/48/48m/min | 48/48/48m/min |
Positioning Accuracy | 土0.008mm | 土0.008mm | 土0.008mm | 土0.008mm |
Repeat Positioning Accuracy | ±0.006mm | ±0.006mm | ±0.006mm | ±0.006mm |
Number of Tools | 16T-21T | 16T-21T | 16T-21T | 16T-21T |
Tool Changing Method | Clamp Arm | Clamp Arm | Clamp Arm | Clamp Arm |
Maximum Tool Diameter | 60 (adjacent no tool. 80) mm | 60 (adjacent no tool. 80) mm | 60 (adjacent no tool. 80) mm | 60 (adjacent no tool. 80) mm |
Maximum Tool Length | 250mm | 250mm | 250mm | 250mm |
Maximum Tool Weight | 3kg Partial Load/10kg Full Load | 3kg Partial Load/10kg Full Load | 3kg Partial Load/10kg Full Load | 3kg Partial Load/10kg Full Load |
Handle Type | BT30 | BT30 | BT30 | BT30 |
Tool Change Time | 1.4sec(60Hz) | 1.4sec(60Hz) | 1.4sec(60Hz) | 1.4sec(60Hz) |
Air Pressure Demand | 0.35-0.6kg/cm² | 0.35-0.6kg/cm² | 0.35-0.6kg/cm² | 0.35-0.6kg/cm² |
Maximum Processing Speed | 12000mm/min | 12000mm/min | 12000mm/min | 12000mm/min |
Cooling Pump | 1200W | 1200W | 1200W | 1200W |
Power Requirements | 20kva | 20kva | 22kva | 22kva |
Machine Weight | 3100kg | 3200kg | 3500kg | 4200kg |
Machine Size | 1700*2600(including water tank)*2500mm | 1900*2700(including water tank)*2500mm | 2000*2800(including water tank)*2500mm | 2200"2800(including water tank)"2500mm |
Features of Metal Drilling and Milling Vertical Machining Center
- Up to 21 tools can be clamped at one time, efficiently meeting complex processing needs.
- Use BT30 tool holder, which is compatible with various knives.
- Fully enclosed shell design makes processing more environmentally friendly and pollution-free.
- Use constant power spindle, stable speed and good processing effect.
- Supports manual simulation processing to effectively avoid machine collision.
- Intelligent control system can reduce gear clearance and improve processing accuracy through position compensation.
- High torque motor effectively shortens the positioning time of each axis and improves processing efficiency.
- Automatic water cooling system automatically adjusts the cooling water spray according to the processing status to ensure stable operation of the equipment.
What Industries Can CNC Metal Milling Vertical Machines Be Used In?
- Electronic digital industry: mobile phone metal middle frame, radiator, speaker shell, digital accessories, chip packaging shell, electronic product shell, filter, radiator and other small light metal parts, etc.
- Automotive parts industry: engine parts, body structure parts, battery shell, motor shell, auto parts, auto shell, chassis parts, motor, gear, etc.
- Mold manufacturing industry: mold cavity, small shell parts, copper mold, aluminum mold, etc.
- Aerospace industry: aircraft engine parts, spacecraft shell, aviation model accessories, drone accessories, etc.
- Medical equipment industry: medical device shell, surgical instruments, precision components, etc.
- Railway transportation: rail transportation equipment parts, body frames, bogies, etc.
There are many types of tools for metal drilling and tapping vertical machining centers. Different tools need to be selected according to the characteristics of the parts to be processed. The following is a detailed description of the tools for metal drilling and tapping vertical machining centers:
- Tool type and features:
Milling cutter: used to process the outer surface and contour of parts, such as end mill, ball nose mill, chamfering mill, dovetail mill, T mill, roughing mill, mill for aluminum, polishing mill, 3 flult mill, face mill, etc.
Drill: used for drilling, including spot drill, twist drill, taper drill, C step drill, tower strp drill, etc.
Reamer: used for secondary processing of holes, including rough reamer, taper reamer, etc.
Tap: used for processing threads, including extrusion tap, cutting tap, straight flute tap, spiral flute tap, etc.
- Special purpose tools: such as composite tools, indexable tools, vibration-damping tools, large diameter cutter heads, etc.
- Tool Material:
- High-speed steel: Suitable for processing materials with lower hardness such as steel, aluminum alloy and copper. It is cheap and has lower cost, but its cutting speed and service life are worse than cemented carbide.
- Cemented carbide(TiAlN coating): Suitable for processing materials with higher hardness such as stainless steel, titanium alloy and ceramic, with higher hardness, wear resistance and processing speed.
- Ceramic tools: Suitable for processing materials such as glass, quartz, ceramic, with high hardness and wear resistance, but relatively expensive and easy to break.
- High-precision materials: Such as cubic boron nitride (CBN) and polycrystalline diamond (PCD), suitable for processing high hardness and high viscosity materials such as high manganese steel and cast iron.
Choosing different tools according to different processing requirements can effectively reduce costs and improve processing speed and efficiency.
- When processing hard materials: Such as stainless steel, titanium alloy, hardened steel (HRC45 and above), carbide (such as PCD, CBN) or ceramic tools should be preferred. These materials have high hardness and wear resistance, suitable for efficient and high-speed cutting, but the cost is relatively high.
- When processing softer materials: Such as aluminum alloy, copper, etc., high-speed steel (HSS) tools are usually selected because of their good toughness and heat resistance, and the price is relatively low and the cost is low.
- When processing some special materials: Such as duplex stainless steel, high-temperature alloys, etc., coated carbide tools can be selected to effectively improve wear resistance and corrosion resistance.
The geometric parameters of the tool, such as the blade shape, front edge angle, back edge angle and blade inclination angle, will directly affect the cutting force, cutting temperature and tool life. Reasonable setting of these processing parameters can reduce wear while ensuring processing accuracy. For high-speed cutting, it is recommended to use a tool with a larger front edge angle to reduce cutting resistance and improve heat dissipation performance.
Although carbide tools have a longer service life, they are more expensive, while ordinary high-speed steel tools have a shorter life but are cheaper and less expensive. Therefore, when selecting tools, it is necessary to comprehensively consider processing efficiency, cost and tool replacement frequency. For mass production or long-term production projects, carbide tools can be given priority; for short-term projects or customized small-scale production, high-speed steel tools may be more cost-effective
Model | CK-4060-T6 | CK-7045-T7 | CK-8050-T8 | CK-1050-T10 |
---|---|---|---|---|
X/Y/Z Axis Travel | 600/400/330mm | 700/450/330mm | 800/500/330mm | 1000/500/330mm |
Workbench Size (Length * Width) | 700*420mm | 800*420mm | 1000*500mm | 1100*500mm |
Processing Range | 600*400mm | 700*420mm | 800*500mm | 1000*500mm |
T-Slot (Center Distance * Slot Width * Number of Slots) | 3*14*125mm | 3*14*125mm | 5*18*100mm | 5*18*100mm |
Maximum Load of Workbench | 250kg | 250kg | 350kg | 350kg |
Spindle Nose to Work Table | 150-450mm | 150-450mm | 150-480mm | 150-480mm |
Spindle Center to Column Guide Surface | 460mm | 460mm | 540mm | 540mm |
Spindle Taper | BT30 | BT30 | BT30 | BT30 |
Spindle Speed | 12000/20000rpm | 12000/20000rpm | 12000/20000rpm | 12000/20000rpm |
Spindle Diameter | 105mm | 105mm | 105mm | 105mm |
Spindle Bearing | 4XNSK7010C | 4XNSK7010C | 4XNSK7010C | 4XNSK7010C |
Spindle Drive Mode | Direct Connected | Direct Connected | Direct Connected | Direct Connected |
Spindle Motor | 5.5-7.5kw | 5.5-7.5kw | 7.5kw | 7.5kw |
Cutting Feed (X/Y/Z Axis) | 12000/12000/12000mm/min | 12000/12000/12000mm/min | 12000/12000/12000mm/min | 12000/12000/12000mm/min |
Rapid Feed (X/Y/Z Axis) | 48/48/48m/min | 48/48/48m/min | 48/48/48m/min | 48/48/48m/min |
Positioning Accuracy | 土0.008mm | 土0.008mm | 土0.008mm | 土0.008mm |
Repeat Positioning Accuracy | ±0.006mm | ±0.006mm | ±0.006mm | ±0.006mm |
Number of Tools | 16T-21T | 16T-21T | 16T-21T | 16T-21T |
Tool Changing Method | Clamp Arm | Clamp Arm | Clamp Arm | Clamp Arm |
Maximum Tool Diameter | 60 (adjacent no tool. 80) mm | 60 (adjacent no tool. 80) mm | 60 (adjacent no tool. 80) mm | 60 (adjacent no tool. 80) mm |
Maximum Tool Length | 250mm | 250mm | 250mm | 250mm |
Maximum Tool Weight | 3kg Partial Load/10kg Full Load | 3kg Partial Load/10kg Full Load | 3kg Partial Load/10kg Full Load | 3kg Partial Load/10kg Full Load |
Handle Type | BT30 | BT30 | BT30 | BT30 |
Tool Change Time | 1.4sec(60Hz) | 1.4sec(60Hz) | 1.4sec(60Hz) | 1.4sec(60Hz) |
Air Pressure Demand | 0.35-0.6kg/cm² | 0.35-0.6kg/cm² | 0.35-0.6kg/cm² | 0.35-0.6kg/cm² |
Maximum Processing Speed | 12000mm/min | 12000mm/min | 12000mm/min | 12000mm/min |
Cooling Pump | 1200W | 1200W | 1200W | 1200W |
Power Requirements | 20kva | 20kva | 22kva | 22kva |
Machine Weight | 3100kg | 3200kg | 3500kg | 4200kg |
Machine Size | 1700*2600(including water tank)*2500mm | 1900*2700(including water tank)*2500mm | 2000*2800(including water tank)*2500mm | 2200"2800(including water tank)"2500mm |
YOU MAY ALSO LIKE
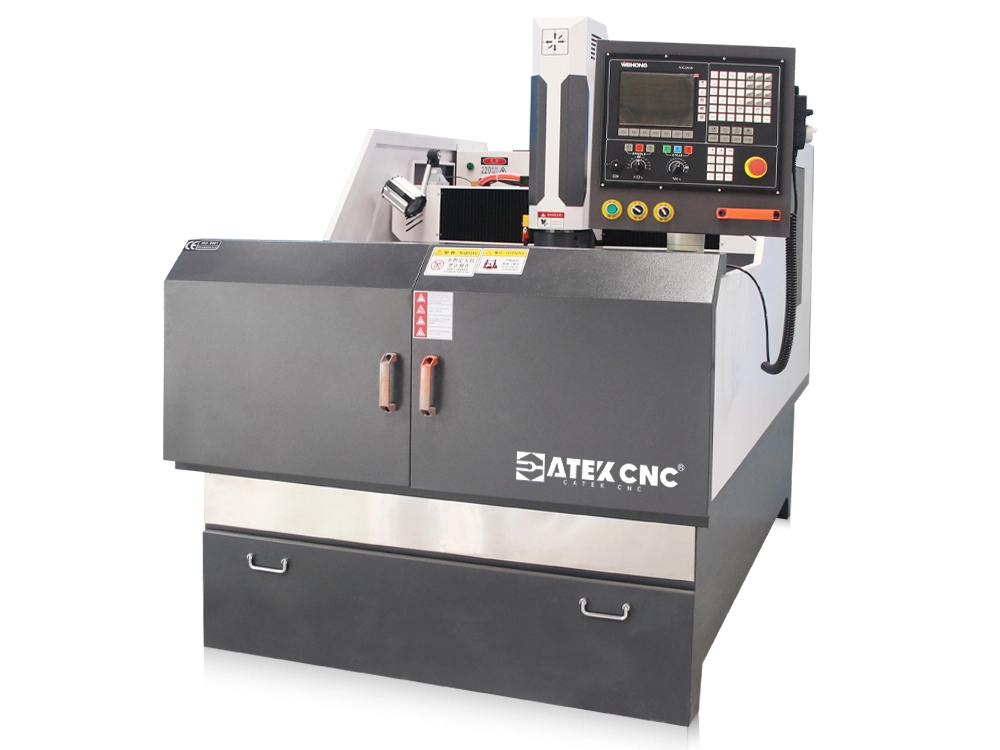
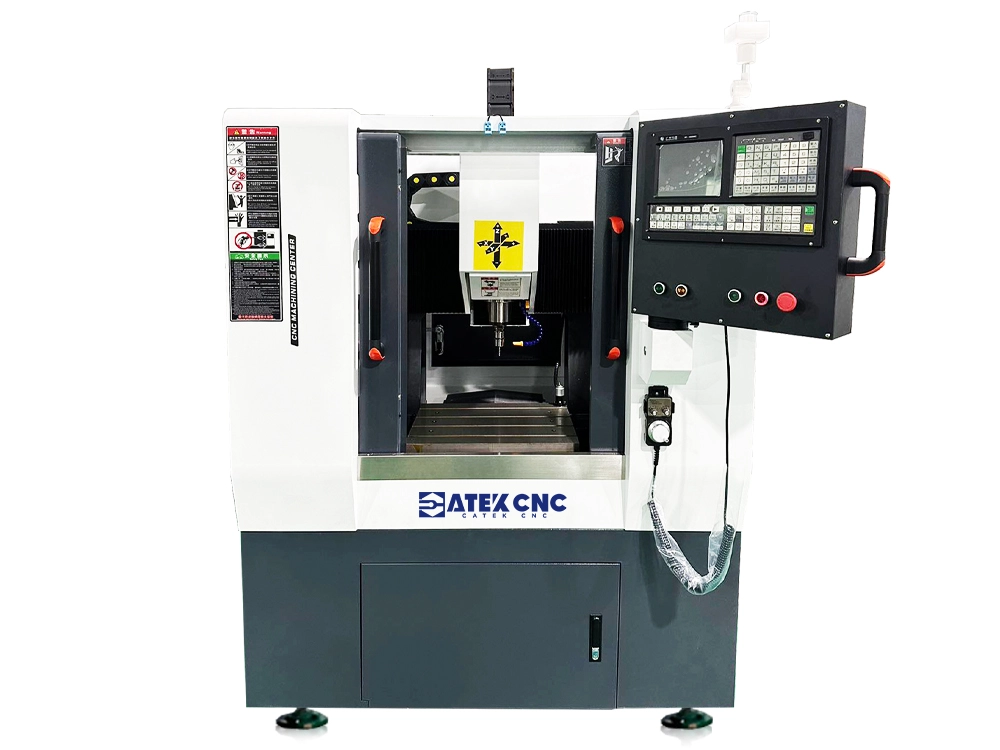
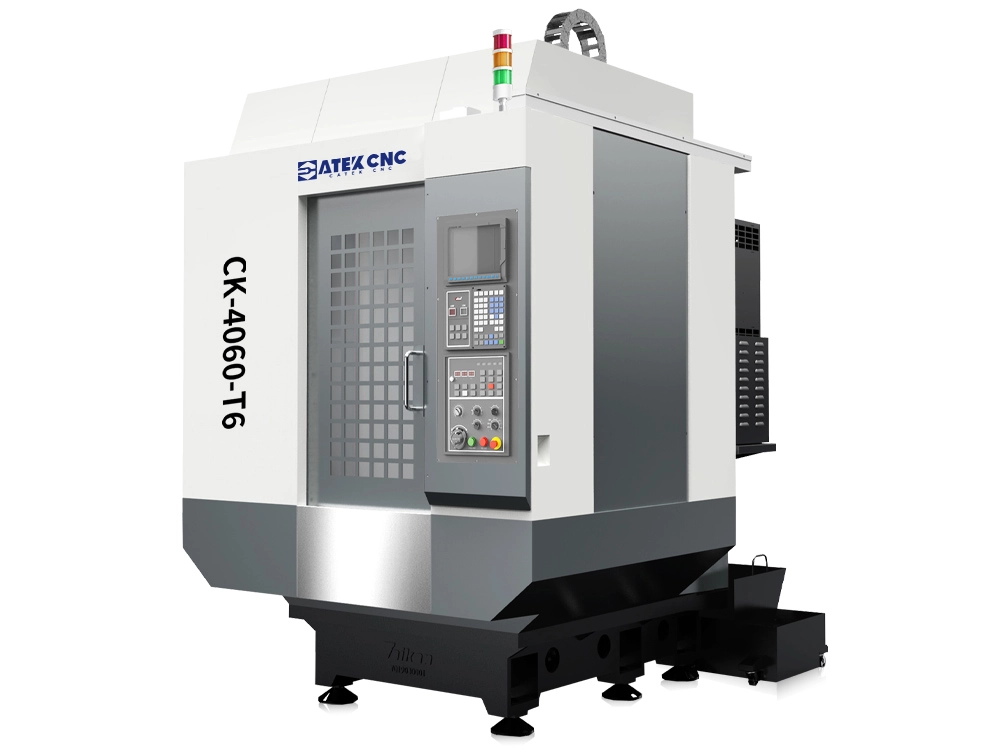
REVIEWS
Let more people know what you share.