Bridge-Type Five-Axis CNC Large 3D Model Making Machine
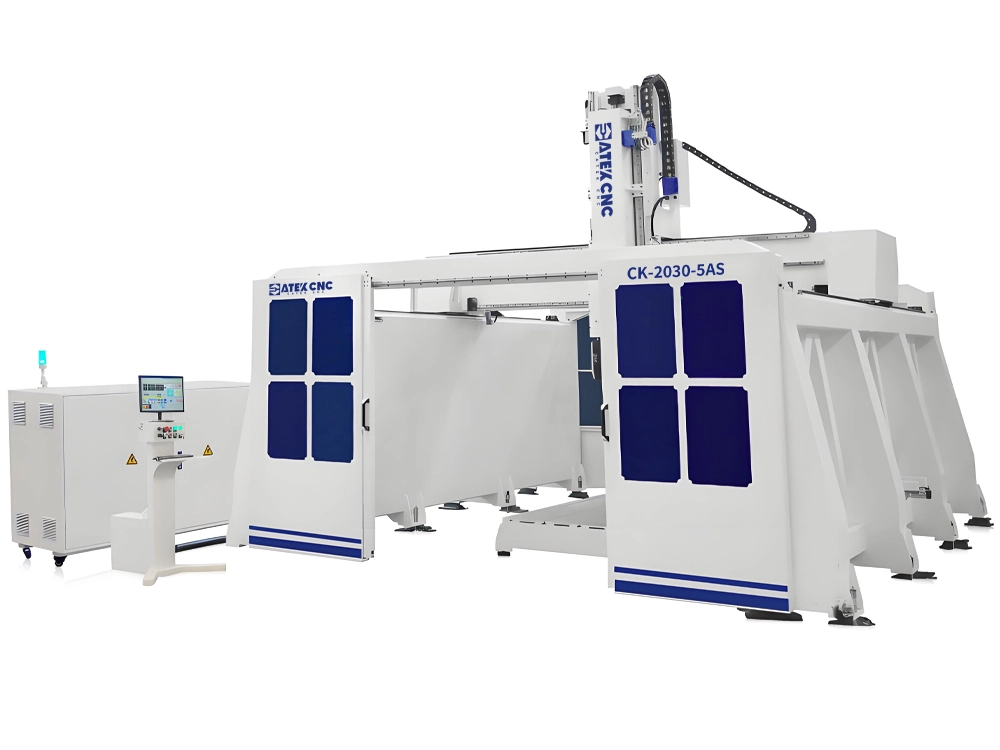
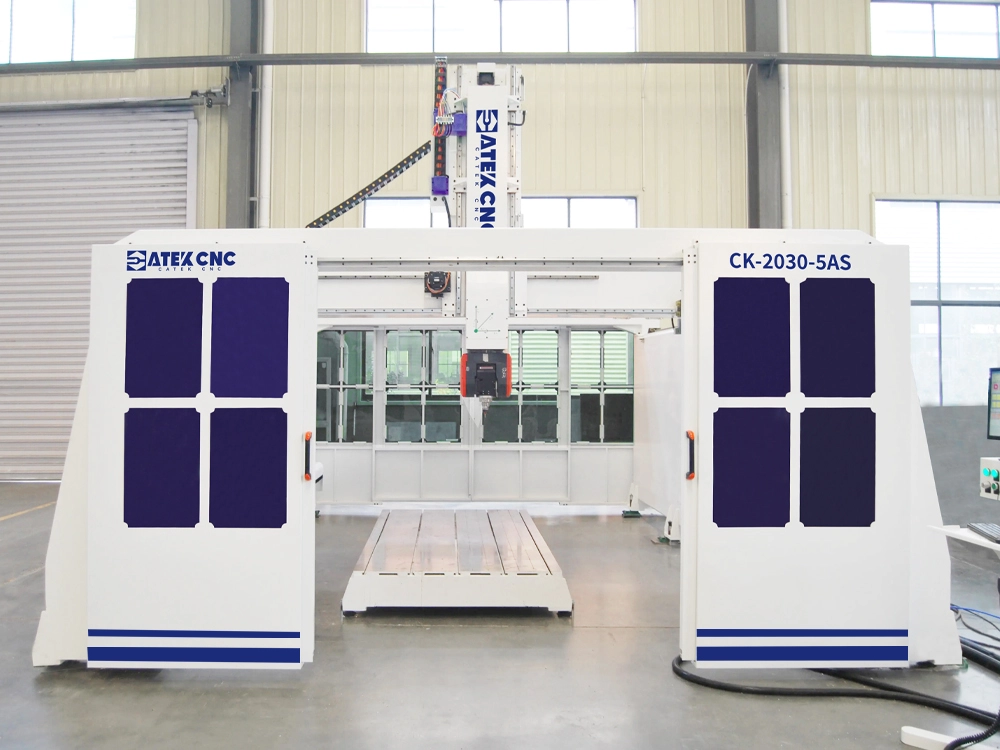
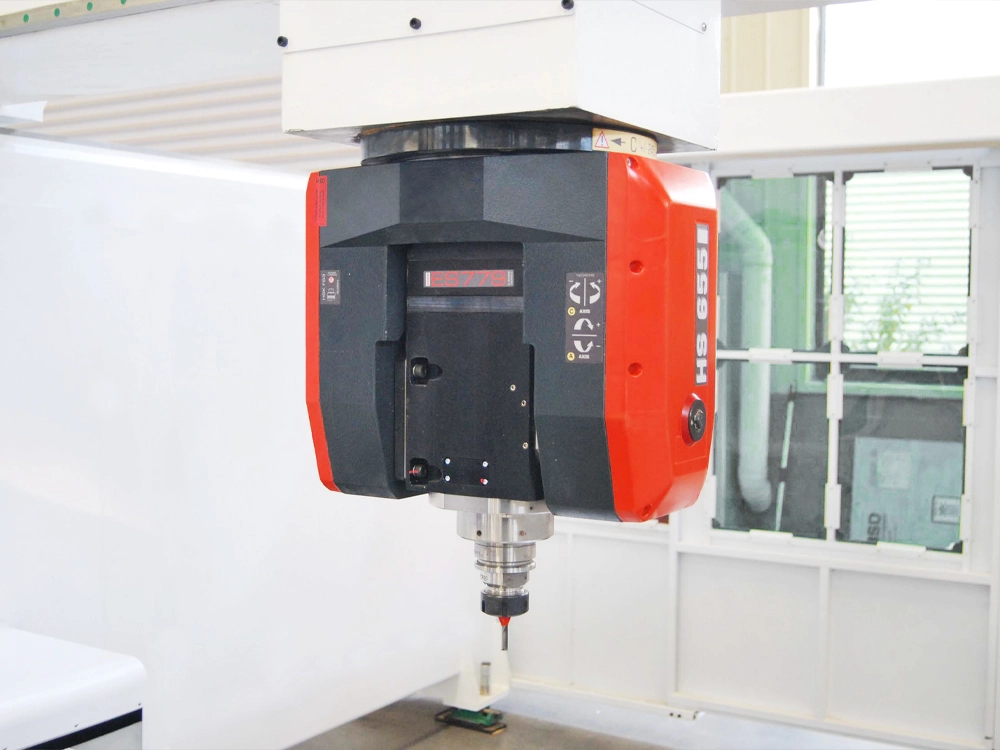
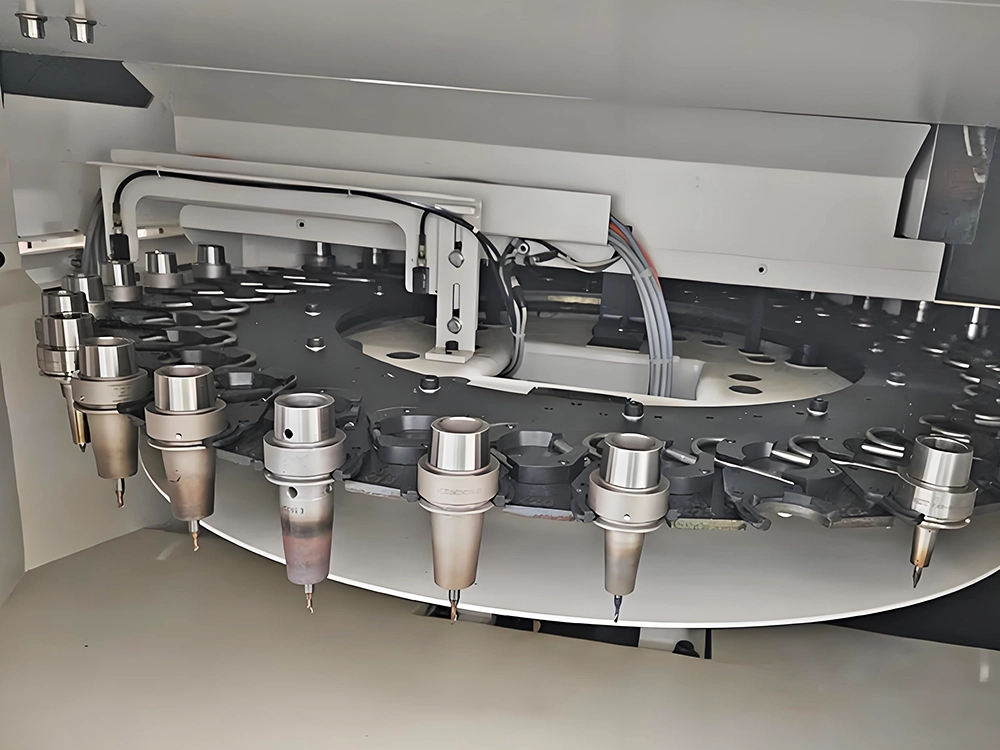
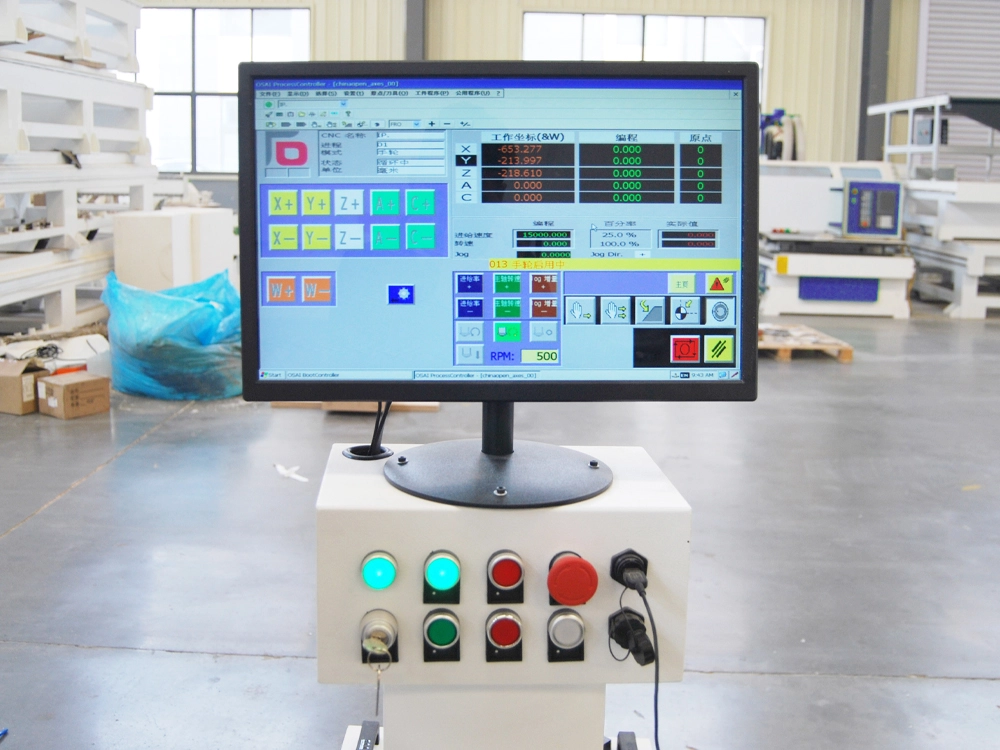
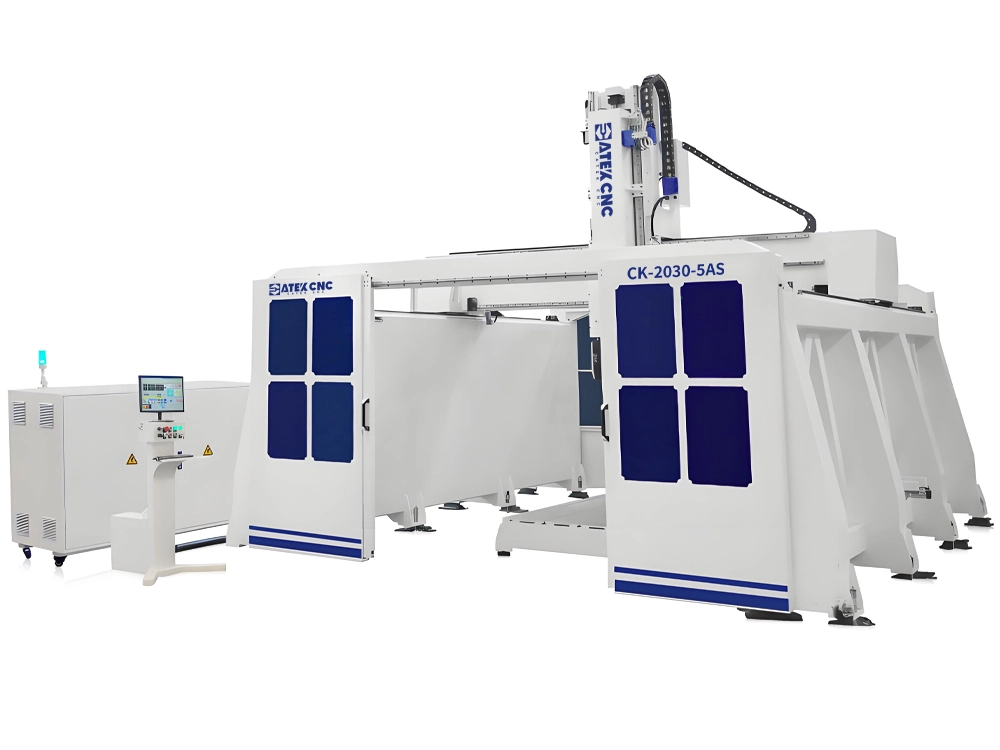
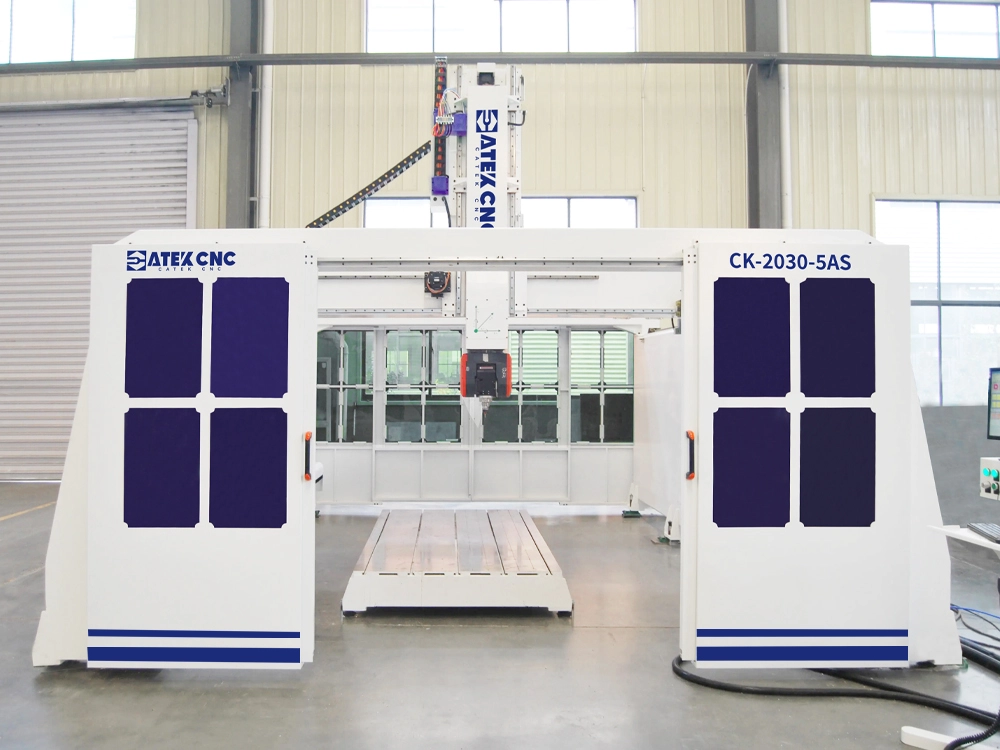
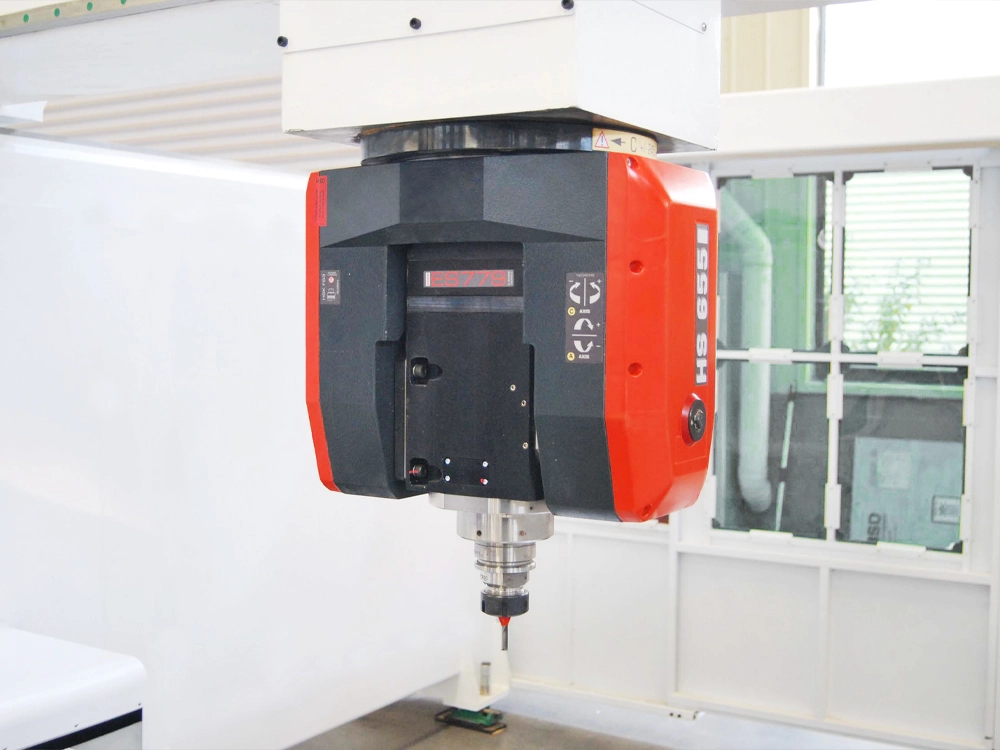
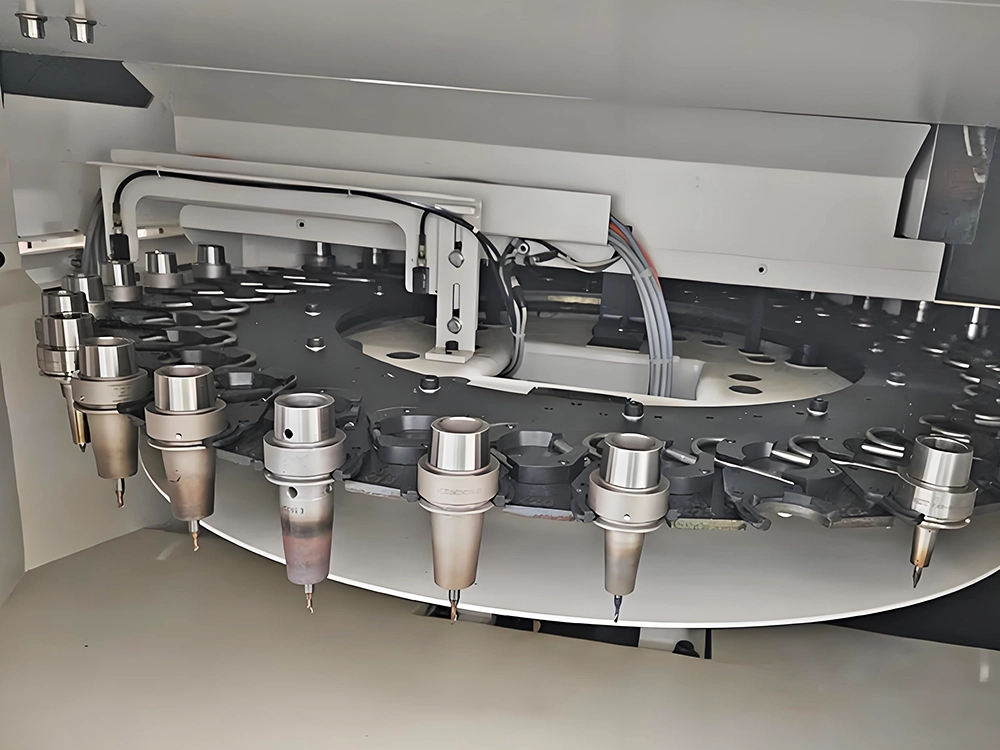
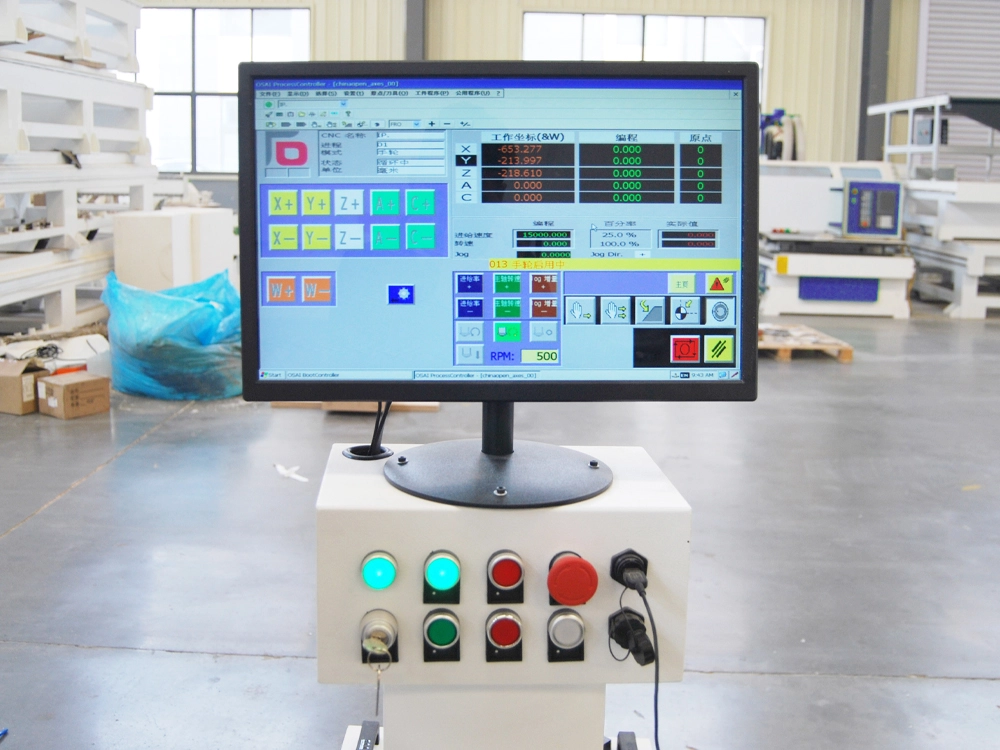
Bridge-Type Five-Axis Large CNC Wood Machining Center for 3D Milling
[Function Description]
The CK-2030-5SA is a high-end five-axis CNC machine that combines five-axis linkage CNC technology with a large-span bridge structure.This machine shares a similar structure with ordinary three-axis routers but adopts a bridge structure, with a large-span overhead rail installed above the bridge that moves along the Y-axis. This design provides a larger machining range on the X, Y, and Z axes, along with better mechanical rigidity and stability, enabling it to withstand greater cutting forces and making it more suitable for processing large workpieces.
Five-axis linkage machining allows for 360°(except the bottom) multi-directional, dead-angle processing of parts in a single setup. It is equipped with three linear axes (X, Y, Z) and two rotary axes (A, C), which can coordinate movements simultaneously. Its three linear axes are the same as those of a three-axis router (except that the beam moves on elevated bridge-style fixed columns), while the two rotary axes are located on the transverse slide. One rotary axis enables circular rotation, and the other allows the machining tool to tilt at a certain angle. This design enables the machine to process workpieces at any angle except the placement surface, achieving complex curved surfaces and multi-dimensional shapes, thereby improving machining accuracy and efficiency.
This five-axis CNC router uses an Italian HITECO/HSD automatic tool-changing spindle and a Japanese Yaskawa servo drive system, with a spindle speed of up to 24,000 rpm. The X/Y/Z axis travel range can be customized from 1,000mm to 6,000mm. Additionally, it supports RTCP (Rotational Tool Center Point) functionality to compensate for coordinate changes caused by the complex spatial movements of the five-axis system.
What is the RTCP Function?
RTCP (Rotation of Tool Center Point) is a key technology in high-end CNC systems, primarily used in five-axis machining centers. Its core function is to compensate in real-time for deviations caused by the movement of one or more axes through the coordinated motion of other axes, ensuring that the tool tip consistently follows the programmed trajectory, thereby improving machining accuracy and efficiency.
Basic principle:
In five-axis machining, the complex spatial movement of the tool center requires the coordinated motion of all five axes. Due to the continuous rotation and angular rotation of the tool, additional motions are generated, causing the tool tip trajectory to deviate from the programmed path, leading to machining errors and reduced precision. The RTCP function compensates for these additional motions in real-time, ensuring the tool tip always follows the programmed trajectory. When programming for five-axis CNC, there is no need to consider the complex movements of the machine's axes; only the relative motion between the tool tip and the workpiece surface needs to be considered. The system automatically handles the complex compensation. The RTCP function is particularly crucial for high-precision, complex machining tasks such as molds and aerospace components, ensuring the accuracy of the tool path and avoiding defects caused by errors.
Key features of the RTCP function:
- Automatic Compensation for Additional Motions: The RTCP function can correct the tool's additional motions in real-time, ensuring the tool tip trajectory matches the programmed path, thereby avoiding machining deviations and improving part accuracy.
- Simplified Programming Process: With RTCP enabled, programmers do not need to manually adjust tool lengths or perform complex calculations. The system automatically handles compensation, effectively simplifying programming tasks, reducing labor intensity, and improving efficiency.
- Enhanced Machining Accuracy and Efficiency: The RTCP function effectively reduces non-linear errors, improving surface finish and dimensional accuracy while shortening machining time, thereby enhancing product quality and overall machining efficiency.
Features of Bridge-Type Five-Axis Large CNC Router
- High-strength bed, using high-temperature annealing process and advanced welding technology, with surfaces milled by heavy-duty gantry milling machines. The internal structure is designed with high-strength anti-stretch and anti-deformation features to ensure the machine body remains stable and does not deform, preventing micro-vibrations during operation.
- Equipped with a single-arm five-axis head, which allows the use of extended tools for machining concave and convex deep surfaces, avoiding interference caused by tool extension rods. The single-arm five-axis head greatly enhances the machine's machining capabilities, enabling milling, drilling, cutting, and other processes at any angle.
- The five-axis head requires high torque, so a Taiwan Murata RV reducer is used, ensuring smooth operation, low energy loss, and suitability for prolonged continuous machining.
- Japanese Yaskawa servo motors, offering excellent performance, fast response, low noise, and good stability, capable of withstanding up to 30 times the load without vibration.
- Taiwan Syntec (five-axis) CNC control system (with RTCP function), featuring powerful functions, high control precision, and simple operation.
- Italian HITECO/HSD 10KW automatic tool-changing spindle, using ceramic bearings for stable rotation speed, equipped with automatic sensors for more intuitive observation of the spindle's motion status.
- Uses HSK 63F/63A tool holders, equipped with a carousel-type automatic tool-changing device, with an multiple-tool capacity for more convenient tool changes.
- TBI high-precision ball screws, offering high operational efficiency, low heat generation, high-speed feed, high positioning accuracy, precise repeat positioning, low friction, and the ability to maintain machining accuracy over long periods.
- Taiwan Hiwin guide rails, featuring high positioning accuracy, low friction coefficient, suitability for high-speed motion, and the ability to maintain high precision in complex environments, making them suitable for various working conditions.
- High-pressure automatic lubrication oil injector, providing higher working pressure than low-pressure oil injectors, meeting the lubrication needs of large machining center machinery.
- Equipped with RTCP function, the machine can automatically compensate for tool offsets, improving machining accuracy and significantly reducing programming complexity.
Details of Bridge-Type Five-Axis Large CNC Router
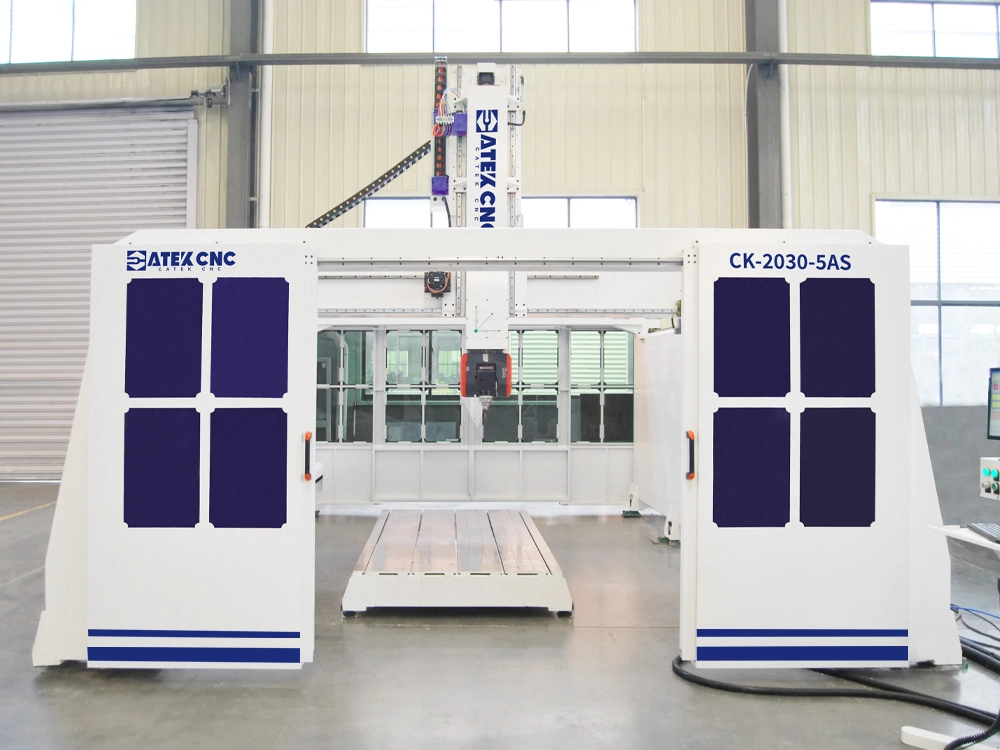
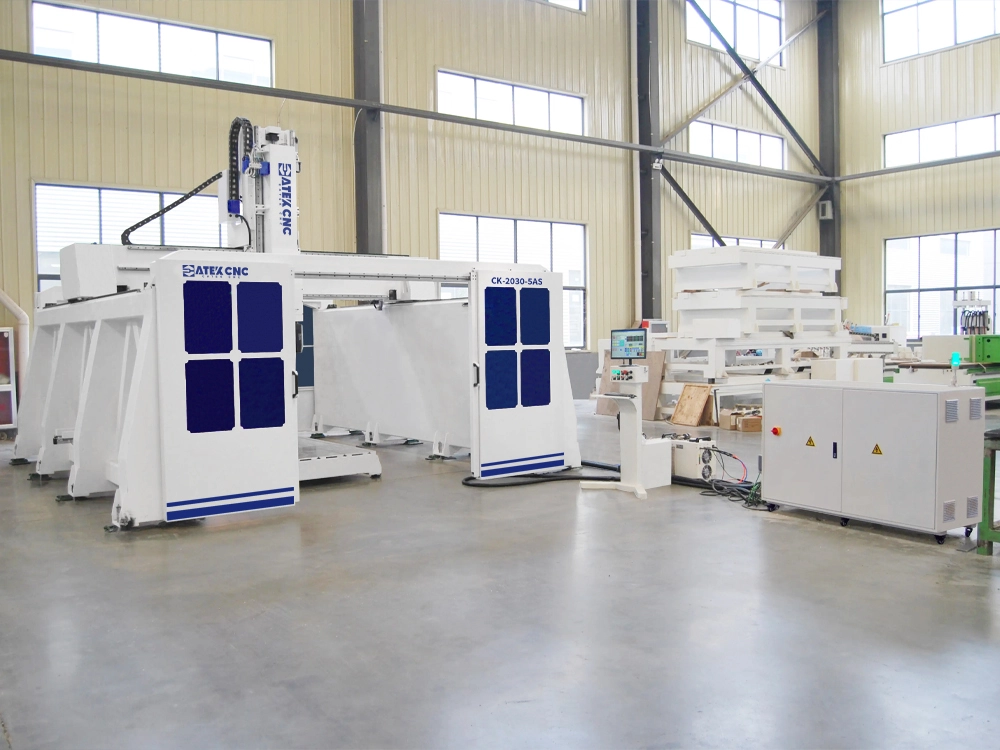
- Five-axis machine head and automatic tool change spindle
A variety of five-axis machine heads and spindle combinations are available.
- Carousel tool magazine
The carousel tool changer can realize automatic switching of multiple tools at a time. It uses HSK 63F/63A tool holders and can clamp various types of tools.
- Five-axis linkage processing
Five-axis linkage processing, equipped with tool tip following function, can process parts from multiple angles in one clamping, with higher processing efficiency.
- Workbench
Changeable workbench, standard T-slot table top, optional vacuum adsorption table top or composite table top.
- Servo motor
Yaskawa servo motors have extremely high precision, quick response, fast start and stop and speed change, and strong stability.
- Control cabinet
Independent control cabinet to avoid electromagnetic interference and facilitate maintenance.
- Control system
Multiple five axis control systems are available for selection
Technical Parameters of Bridge-Type Five-Axis Large CNC Router
Model | CK-2030-5AS |
---|---|
XYZ Work Schedule | 2000*3000*1200mm (customizable according to processing requirements) |
Gantry | Thickened steel structure |
Bed | Customized bed with heavy steel pipe welding |
Spindle | Italian HITECO/HSD 10KW automatic tool-changing spindle |
Spindle Speed | 24000rpm |
Tool Magazine | Carousel automatic tool changer |
Shank Model | HSK 63F/63A |
Driving Mode | Japan YASKAWA servo drive |
Frequency Converter | Taiwan Delta inverter |
Table | Aluminum alloy T-slot table (optional: vacuum adsorption platform) |
Transmission Mode | XY axis high-precision ground helical rack drive + Z axis high-precision TBI ball screw drive |
Guideway | Taiwan Hiwin high precision linear square rail / flange slider |
Equipment Cable | Pure copper anti-bending high-flexible cable |
Control System | Italian OSAI/Taiwan Syntec of five-axis CNC system |
Lubrication System | Electric oil injection maintenance system |
Compatible Software | Artcam, type3, CAD, CDR, JDpaint, artcam, etc. |
Engraving Instructions | Standard G code, u00, mmg, plt |
Positioning Accuracy | 0.03mm |
Repeat Positioning Accuracy | 0.02mm |
Maximum Processing Speed | 30000mm/min |
Maximum No-Load Running Speed | 60000mm/min |
Weight | 8500kg |
Dimensions | 5500*4600*3700mm |
What Products Can a Bridge-Type Five-Axis CNC Milling Machine Process?
Applicable Materials:
Wood, composite materials, PVC, plastics, acrylic, foam, composite materials.
Applicable Products:
Furniture, wood molds, aluminum molds,vacuum-formed rubber and plastics, ABS, bathroom fixtures, artificial stone, crafts, foam models, polystyrene molds, large character molds, vacuum-formed trays, vacuum-formed shells, large vacuum-formed molds, travel cases, office cases, leisure bags, cover plates, plastic molds, helmets, musical instruments, stair railings, thick vacuum-formed products, automotive parts, refrigerator liners, chassis shells,vacuum-formed shells, foam sculptures, solid wood furniture, yachts, aircraft models, medical equipment, building materials, storage boxes, chair backs, and more.
Technical Advantages of Bridge-Type Five-Axis CNC Machine Tools
- High automation
- The bridge-type five-axis CNC milling machine is a highly automated CNC machining center. Except for the manual clamping of parts, the entire machining process is automatically completed by the CNC machine, including functions such as automatic tool changing and automatic measurement, significantly improving production efficiency.
- High precision and high quality
- The bridge-type five-axis CNC machining center adopts advanced CNC systems and precise servo drive technology, enabling high-precision machining of complex parts in a single setup, reducing error accumulation, and improving machining quality.
- High speed and high efficiency
- Equipped with a high-performance spindle system and high-speed drive system, it can achieve rapid cutting and efficient production, enhancing efficiency and reducing costs.
- Flexibility and adaptability
- The bridge-type five-axis machining center can process parts with complex curved surfaces and multi-dimensional shapes. The five-axis linkage function allows machining from multiple directions of the part, increasing machining flexibility.
- Modular design and customization capability
- Featuring a modular design, it can be customized with components such as tool magazines, rotary tables, worktable machining dimensions, and spindles according to customer requirements, meeting diverse machining needs.
Maintenance of Five - Axis CNC Milling Machine
After daily machining is completed, clean the machine surface, guide rails, sliding surfaces, worktable, and other areas to remove chips, dust, and oil stains. Clean the exterior of the electrical cabinet and ensure the interior is tidy and free of debris.
Check the lubricant level daily to ensure an adequate supply, and promptly add or replace lubricant as needed.
Apply oil to the machine guide rails, sliding plates, and other areas prone to rust to prevent corrosion.
Regularly inspect key components such as the spindle unit, feed drive chain, and automatic tool-changing device.
Avoid stacking debris around the machine tool to prevent damage to the equipment due to abnormal temperature.
Model | CK-2030-5AS |
---|---|
XYZ Work Schedule | 2000*3000*1200mm (customizable according to processing requirements) |
Gantry | Thickened steel structure |
Bed | Customized bed with heavy steel pipe welding |
Spindle | Italian HITECO/HSD 10KW automatic tool-changing spindle |
Spindle Speed | 24000rpm |
Tool Magazine | Carousel automatic tool changer (8 tools) |
Shank Model | HSK 63F/63A |
Driving Mode | Japan YASKAWA servo drive |
Frequency Converter | Taiwan Delta inverter |
Table | Aluminum alloy T-slot table (optional: vacuum adsorption platform) |
Transmission Mode | XY axis high-precision ground helical rack drive + Z axis high-precision TBI ball screw drive |
Guideway | Taiwan Hiwin high precision linear square rail / flange slider |
Equipment Cable | Pure copper anti-bending high-flexible cable |
Control System | Italian OSAI/Taiwan Syntec of five-axis CNC system |
Lubrication System | Electric oil injection maintenance system |
Compatible Software | Artcam, type3, CAD, CDR, JDpaint, artcam, etc. |
Engraving Instruction | Standard G code, u00, mmg, plt |
Positioning Accuracy | 0.03mm |
Repeat Positioning Accuracy | 0.02mm |
Maximum Processing Speed | 30000mm/min |
Maximum No-Load Running Speed | 60000mm/min |
Weight | 8500kg |
Dimensions | 5500*4600*3700mm |
YOU MAY ALSO LIKE
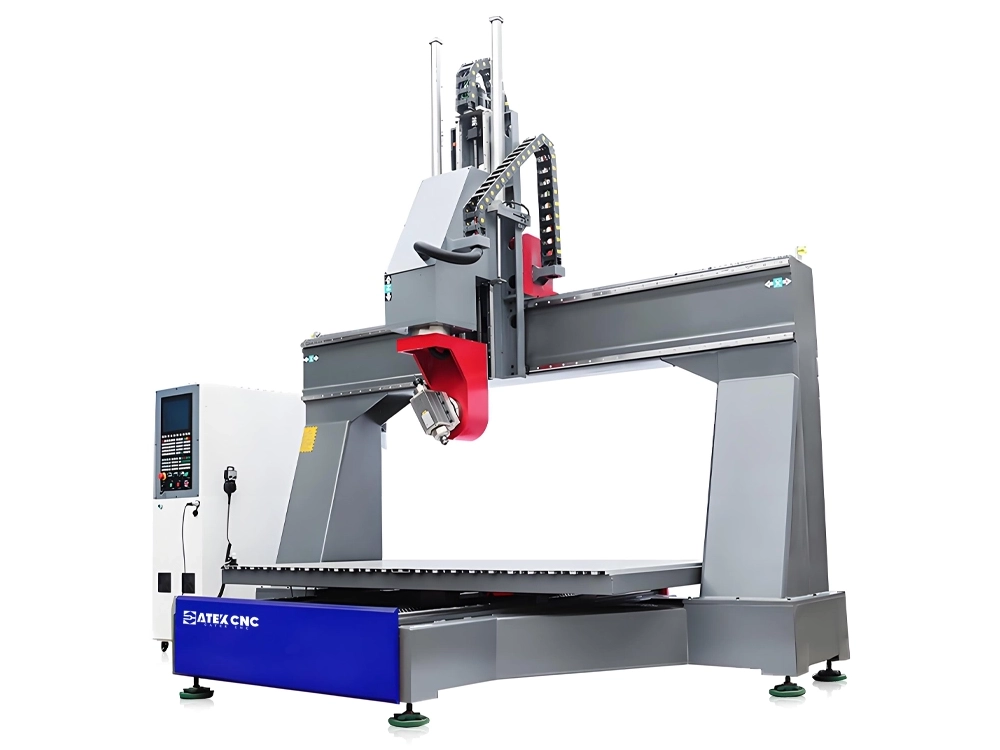
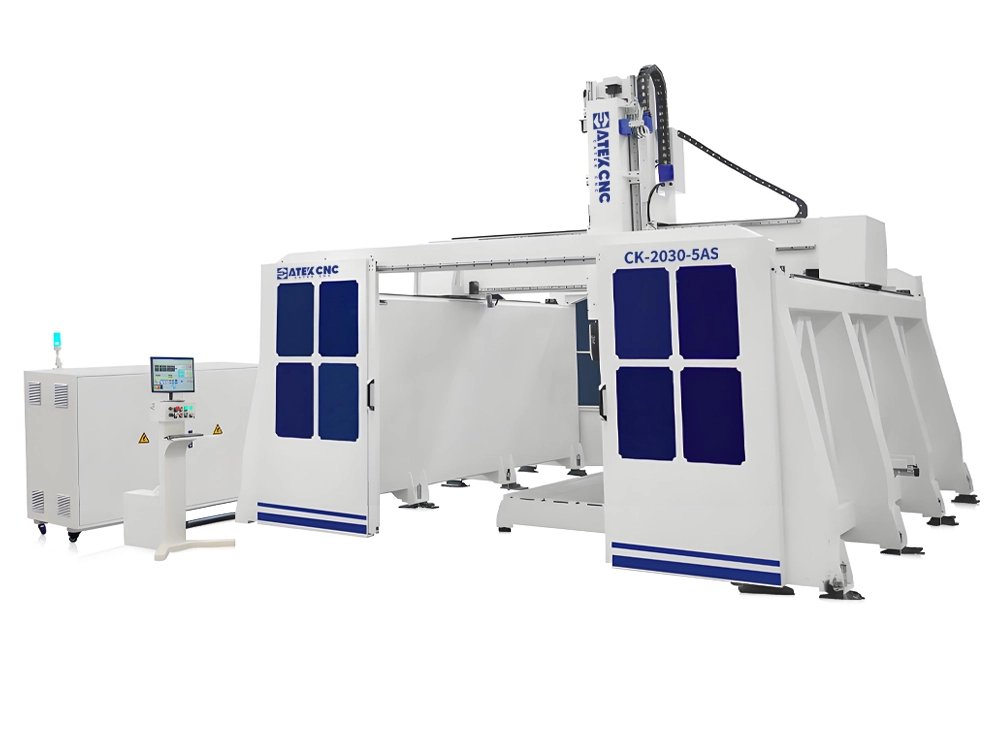
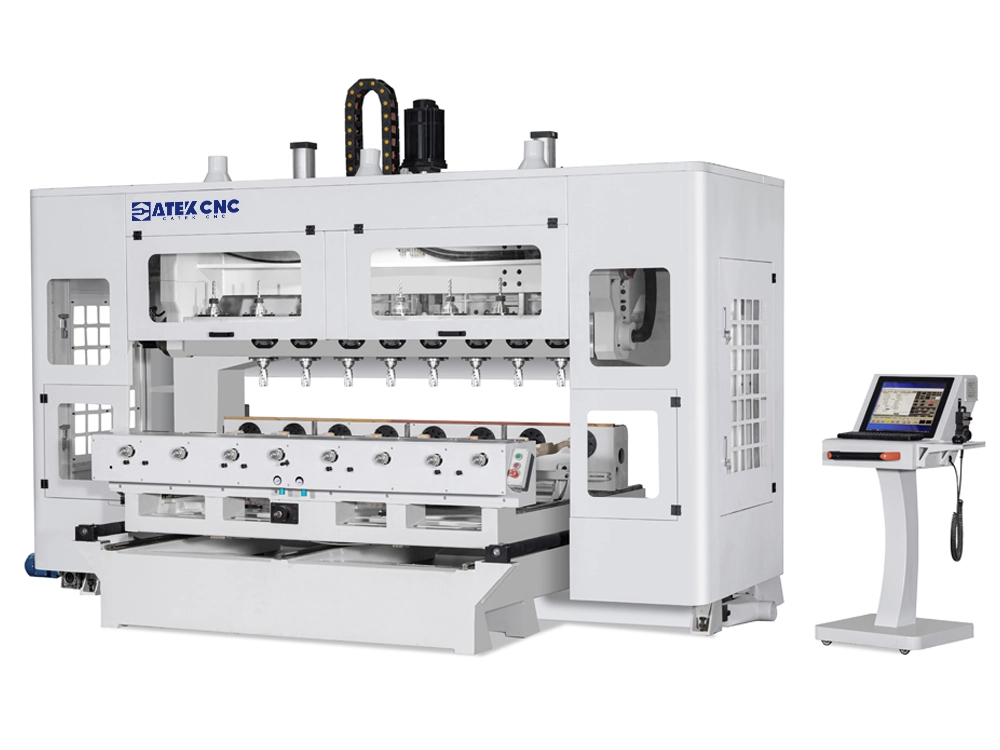
REVIEWS
Let more people know what you share.