Linear Atc CNC Furniture Making Machine Capable of Automatic Drilling, Milling and Grooving
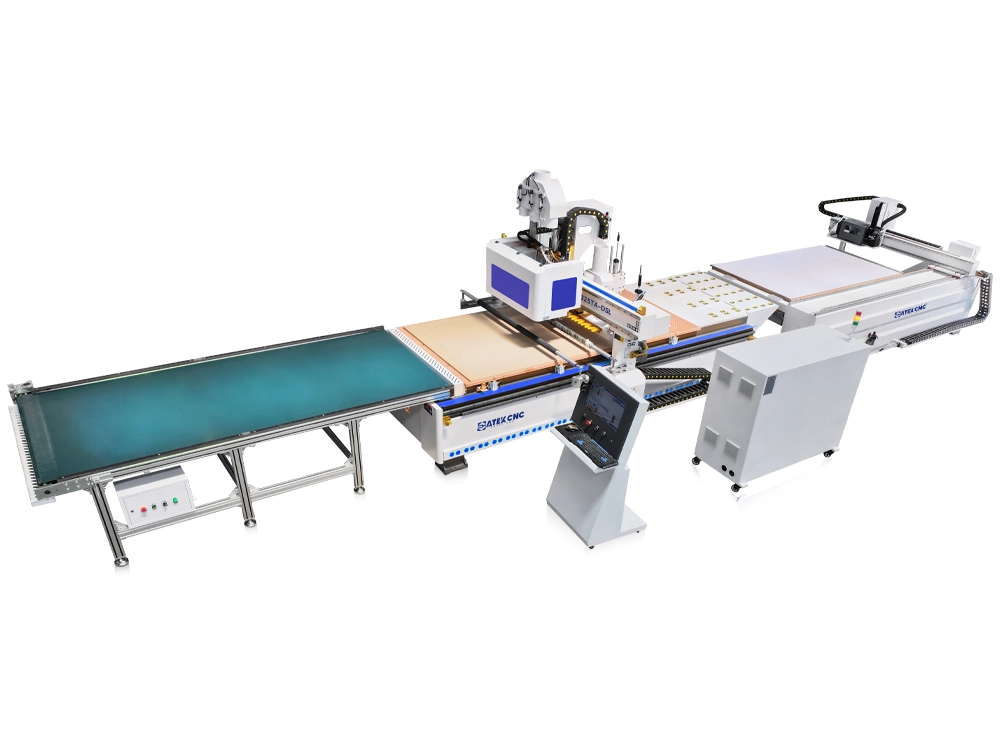
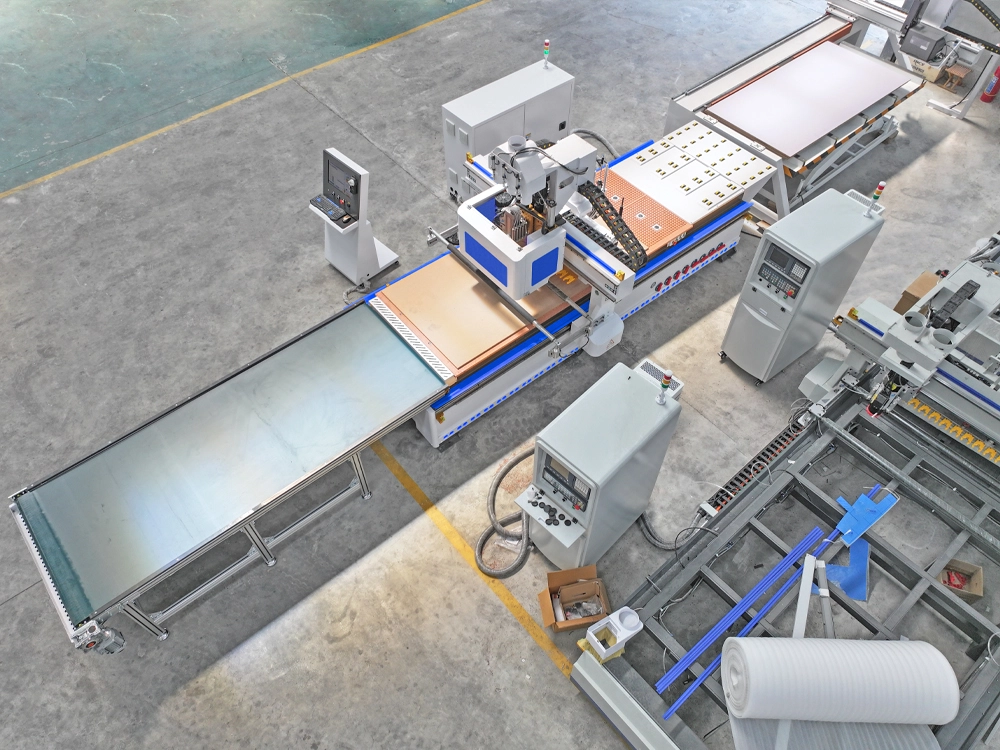
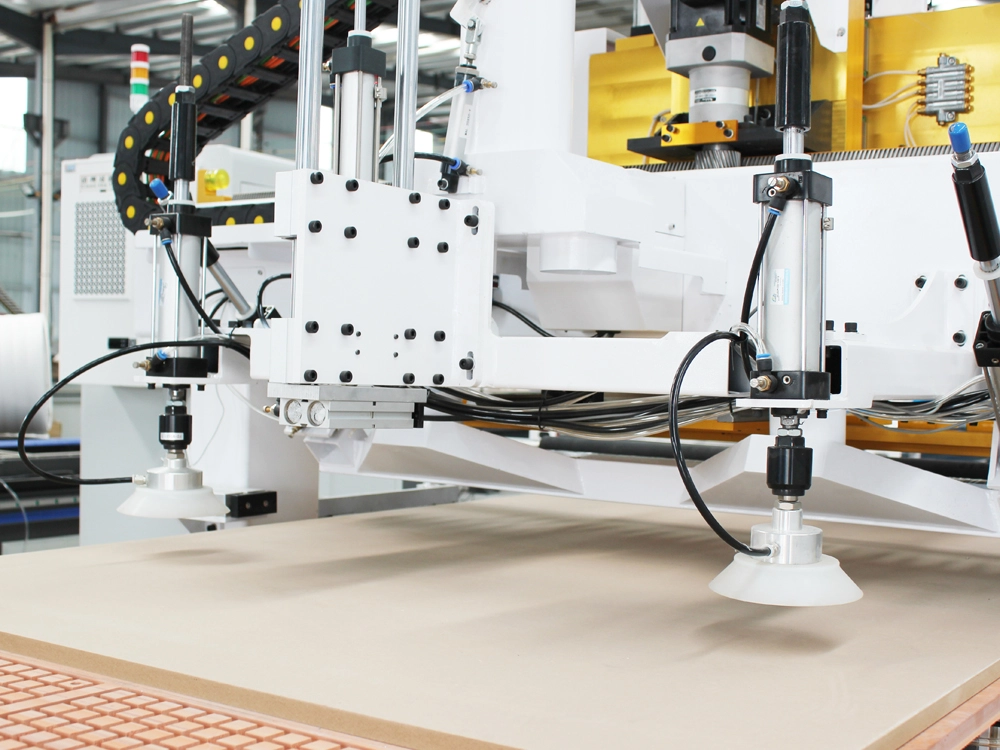
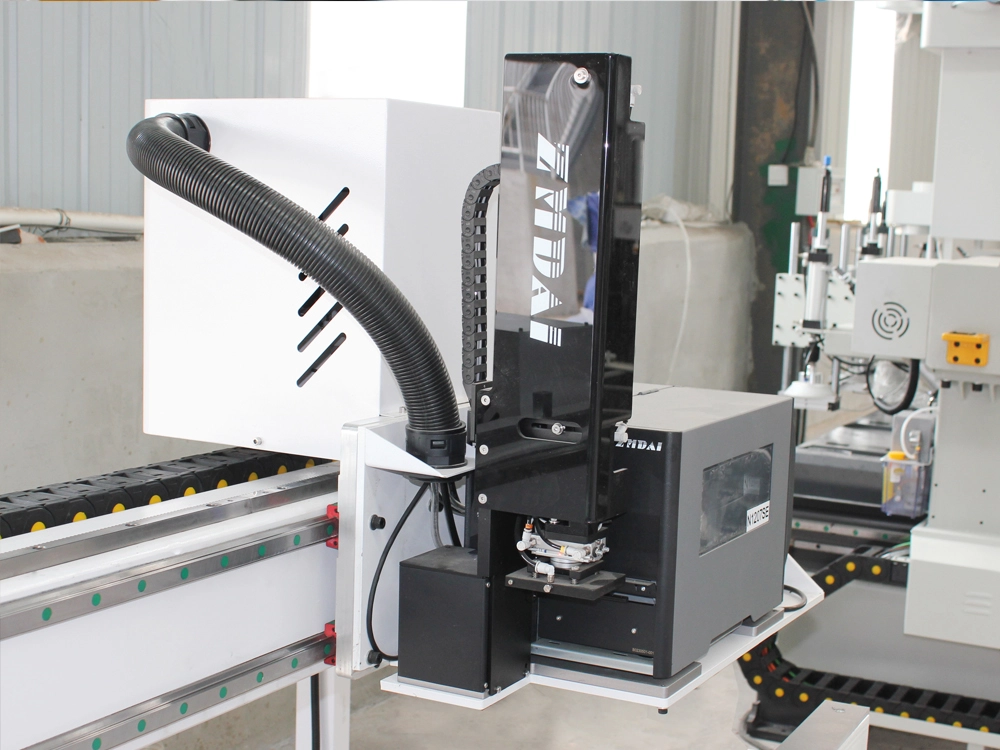
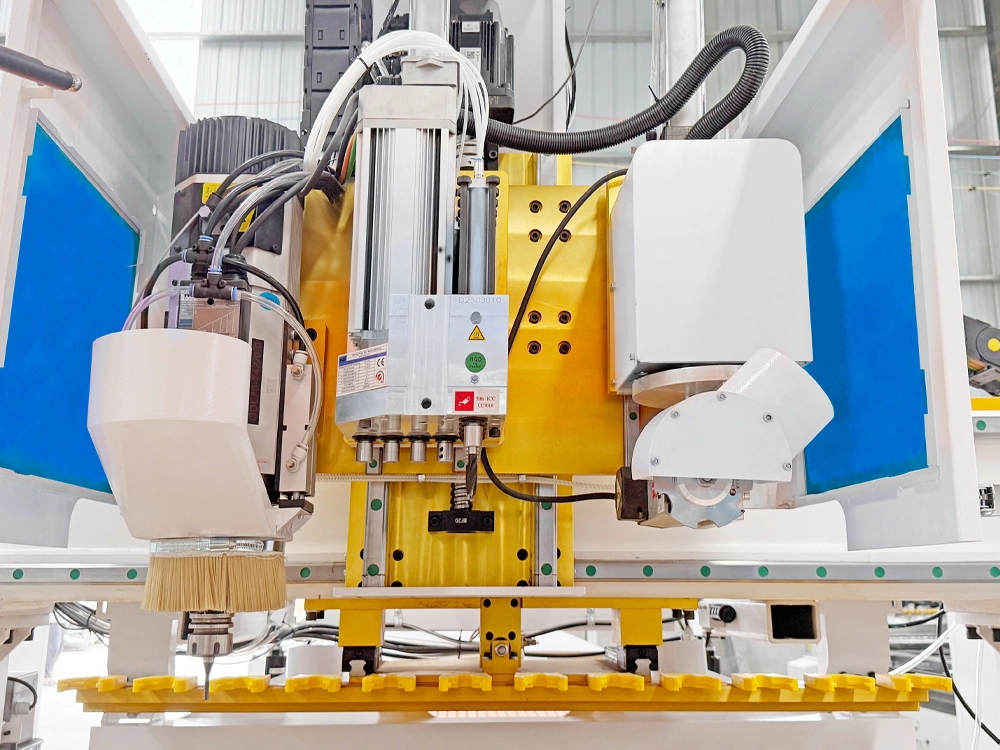
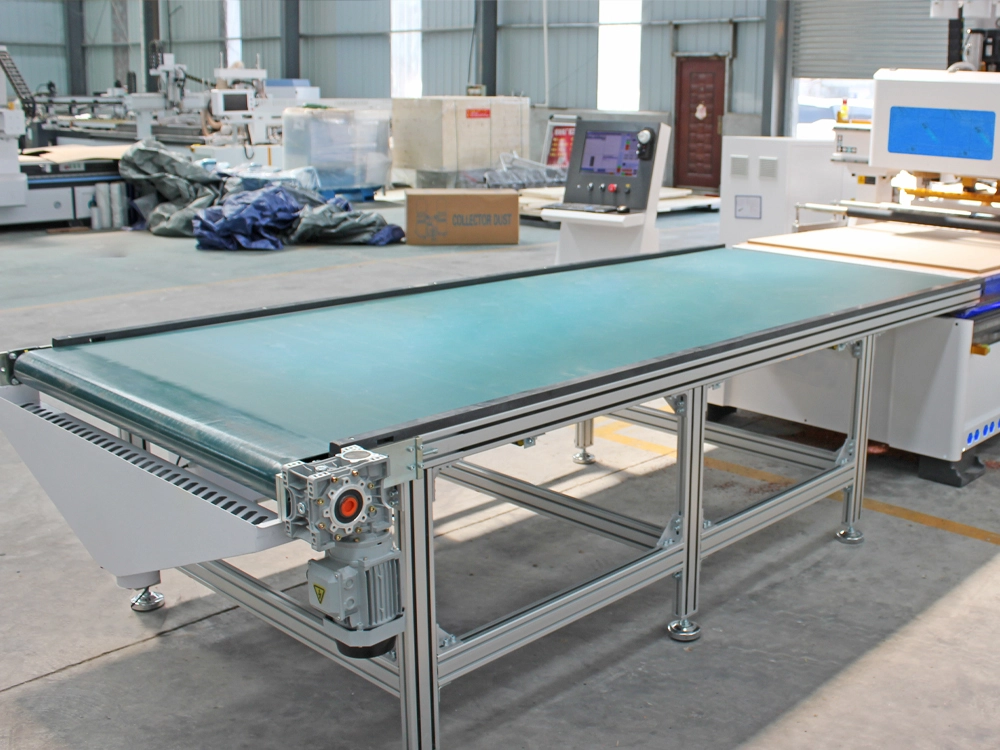
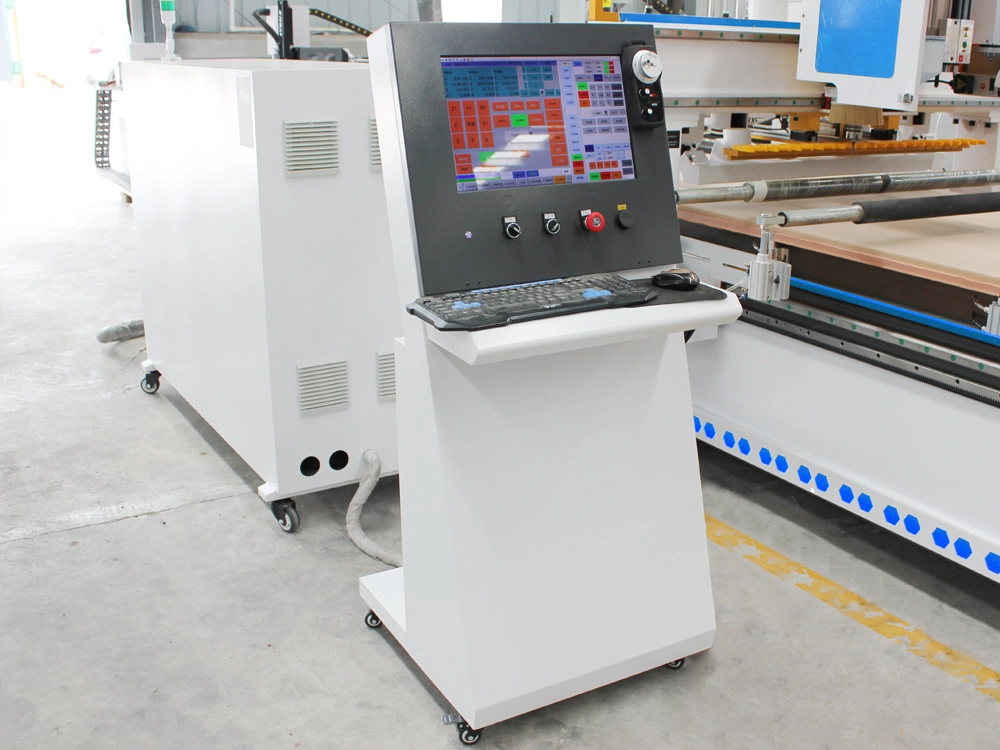
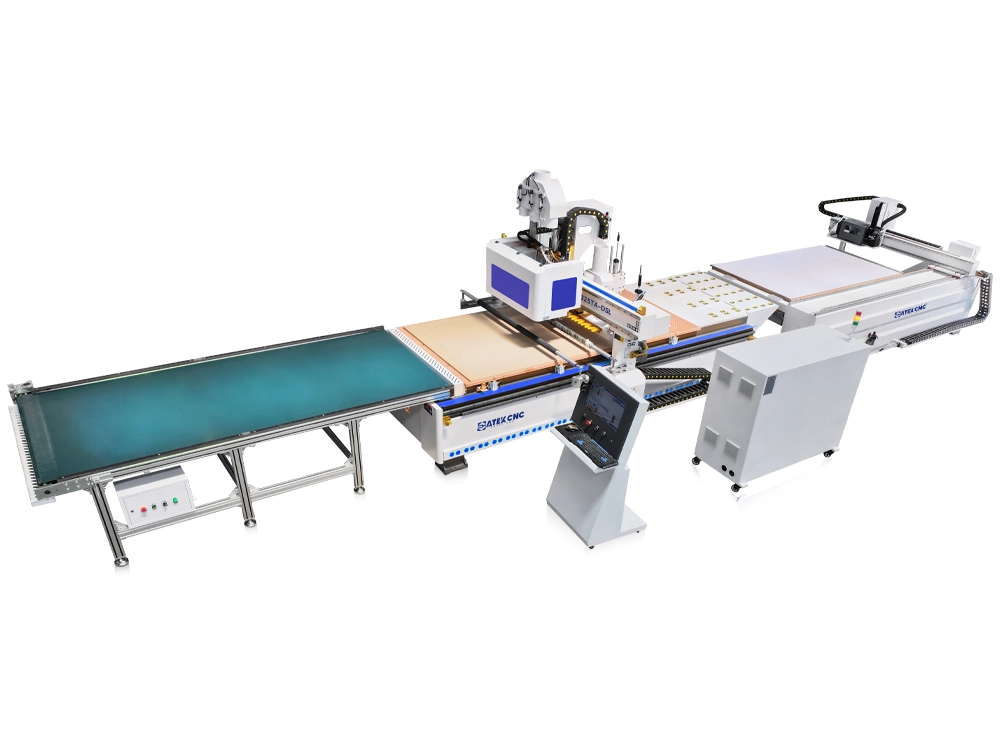
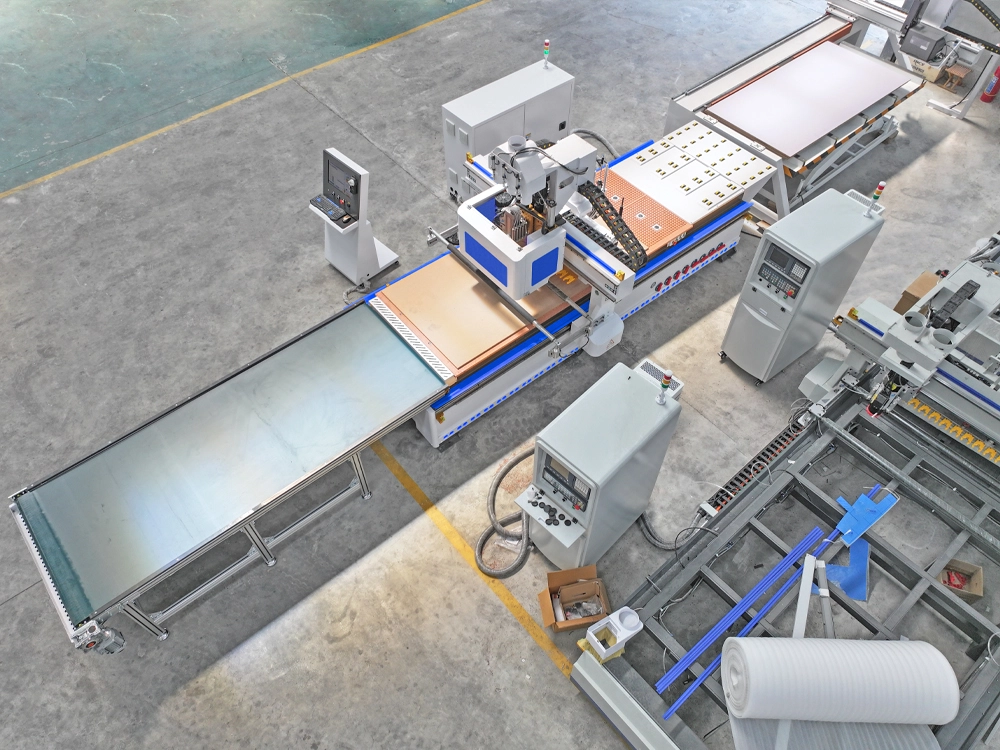
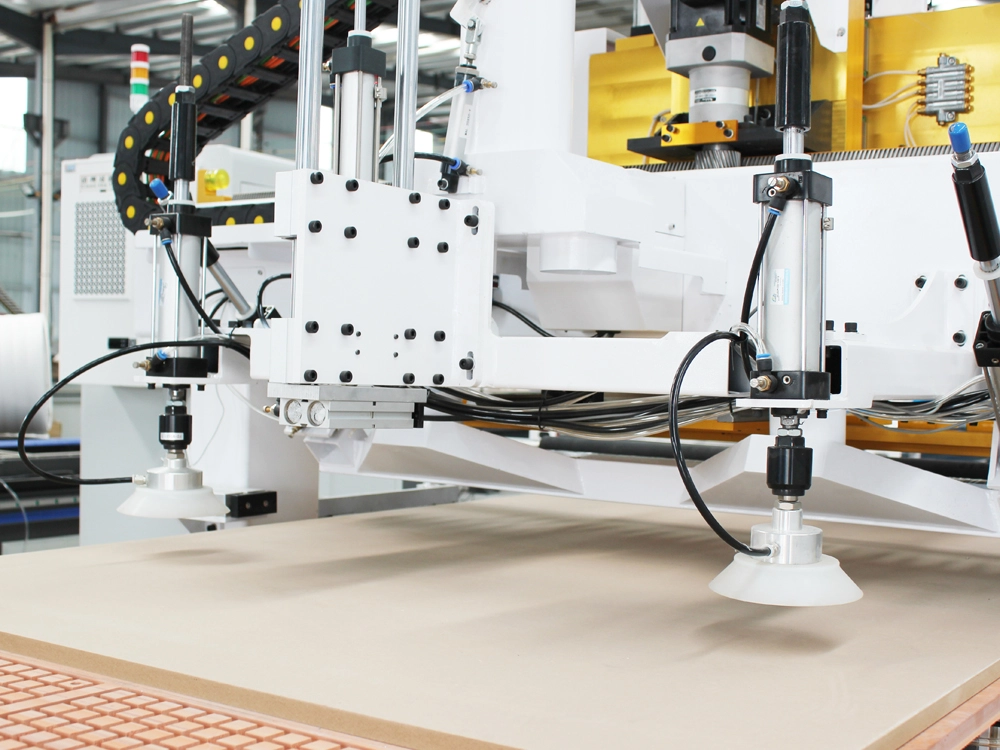
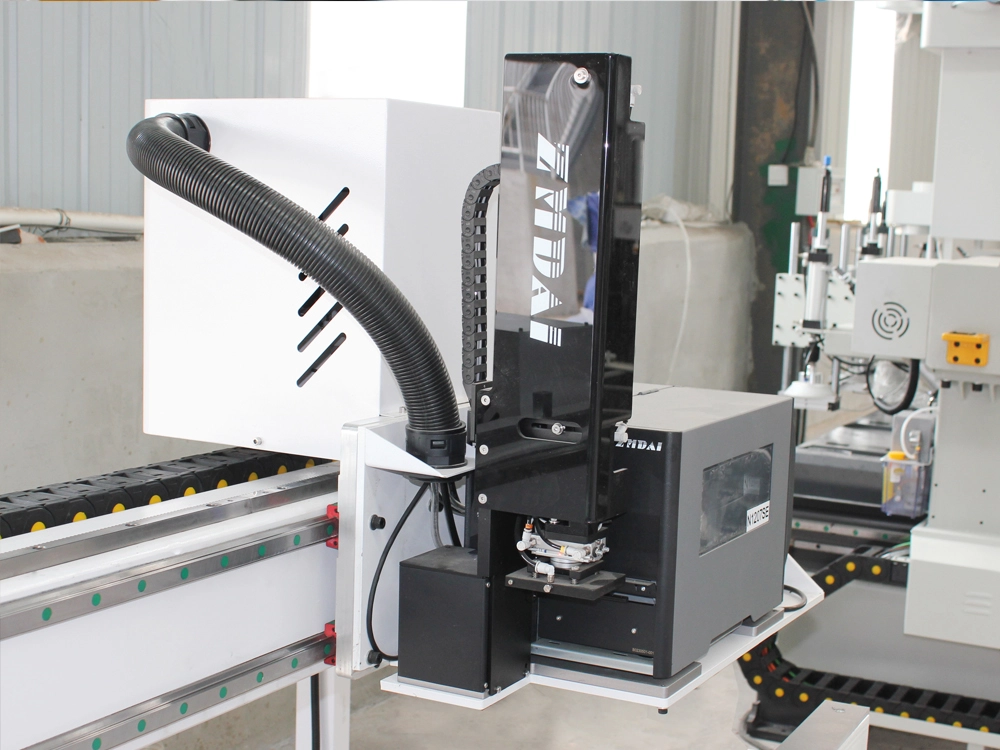
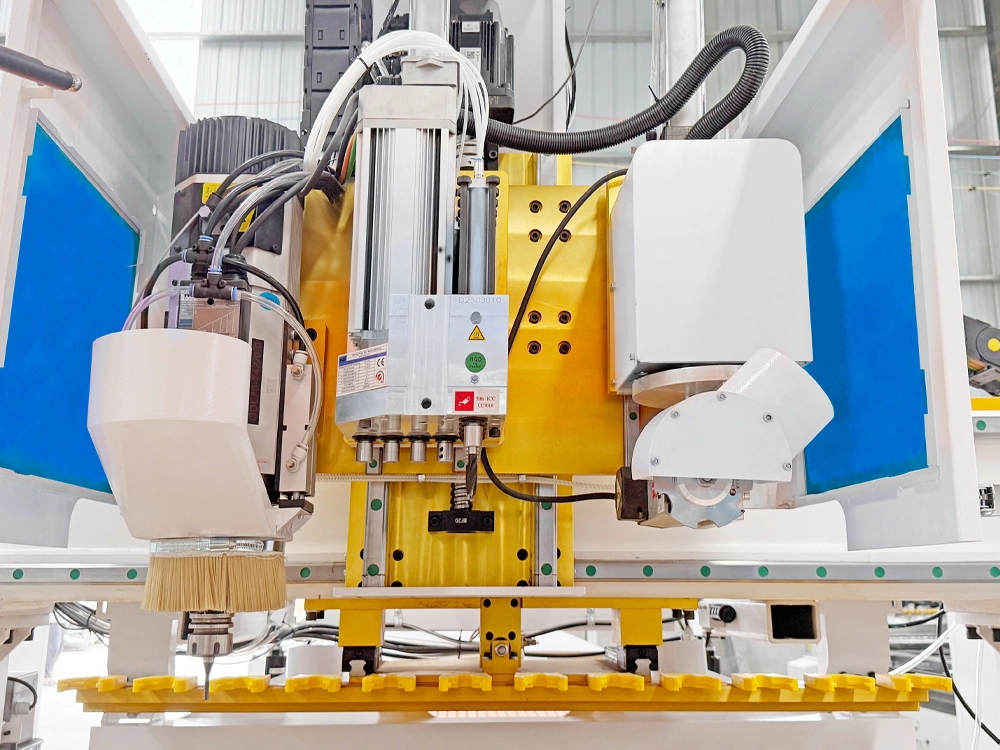
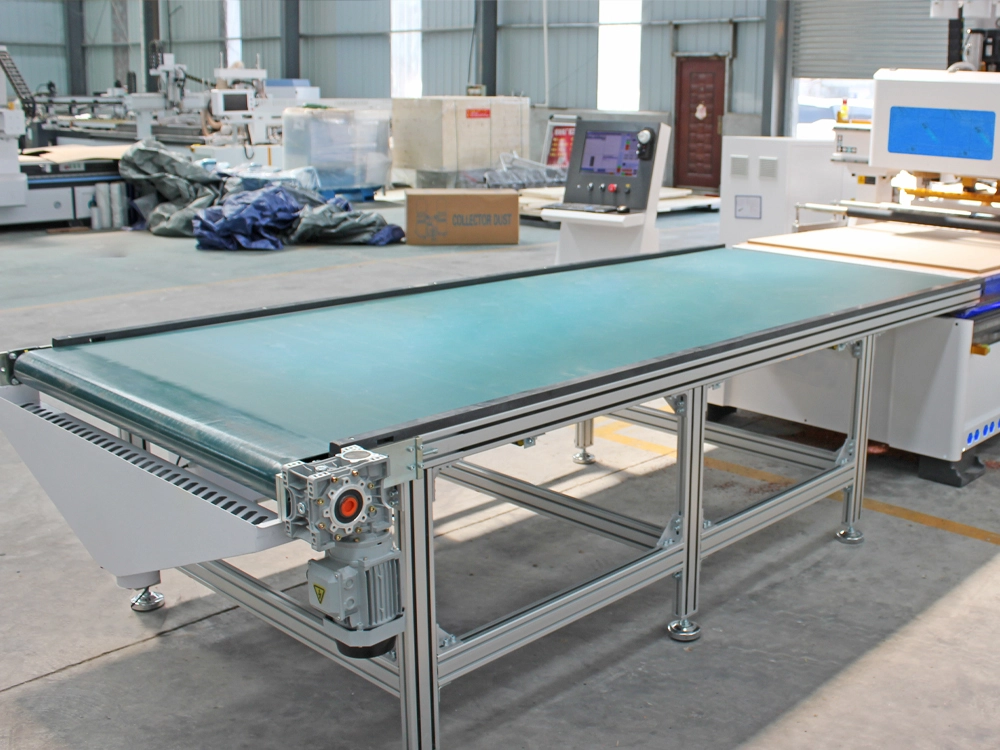
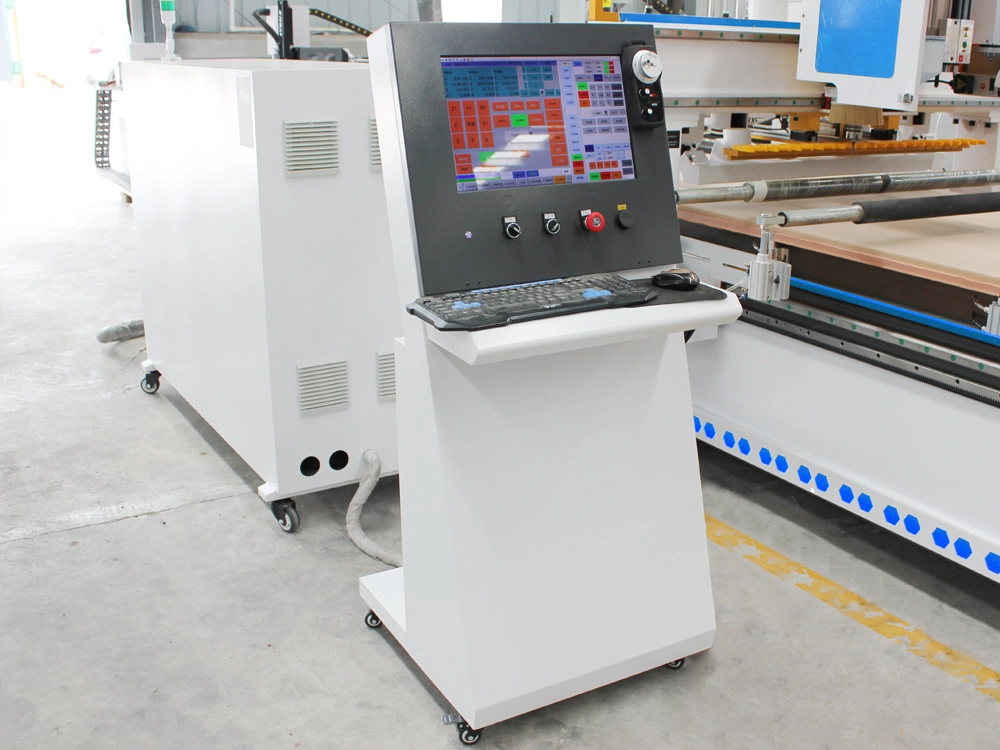
4x9ft CNC Router Machine for Furniture Woodworking Production Line
[Function Description]
The CK-1328TA-DSL is specifically designed for furniture manufacturing plants. It features a 1300×2800mm (4×9 ft) vacuum worktable, a 9KW ATC spindle, a linear tool magazine with 12 tools, an drilling bank, a saw blade for four-axis Lamello invisible connector grooving, and an automatic labeling machine. It also comes with a fully automated loading and unloading platform, enabling seamless integration into production lines to meet all the demands of furniture manufacturing.
During processing, the sheet is first lifted to the labeling area by the automatic lifting platform, where the automatic labeling machine applies labels. Once labeled, the vacuum suction cups pull the sheet onto the vacuum worktable, securing it firmly in place. The machine’s drilling bank and Lamello saw blade then quickly process the required holes and grooves. After grooving and drilling, the ATC spindle performs cutting and milling operations. Once machining is complete, the automatic pusher transfers the sheet onto the conveyor unloading platform for discharge. The entire process is fully automated, eliminating manual intervention, significantly reducing labor costs, and improving processing efficiency.
This CNC woodworking router machine integrates multiple functions, including automatic labeling, loading, nesting, drilling, grooving, milling, engraving, and unloading, making it ideal for high-efficiency production of furniture such as wardrobes and cabinets. Additionally, it is equipped with a comprehensive intelligent dust extraction system, ensuring effective removal and collection of debris and dust throughout the workflow. This makes it exceptionally well-suited for large-scale furniture manufacturing plants.
What Is a CNC Automatic Labeling Machine? How Does It Work?
The automatic labeling machine achieves efficient labeling from label peeling to precise positioning and pasting through the coordinated operation of the control system and sensors. When panel processing begins, the automatic lifting loading platform will automatically adjust the panel to the appropriate height. This process is achieved by infrared photoelectric sensors detecting the panel height signal and transmitting it to the control system. After the panel moves to the preset labeling position, it will automatically trigger the labeling action: the printing device automatically prints the label paper, then precisely conveys the label to the designated position. The pressing suction head picks up the label, descends, and presses the label onto the panel surface. Controlled by the control system, the labeling machine can automatically and quickly complete the entire labeling process from label printing, positioning to pressing, effectively replacing manual labeling. This avoids panel waste or process disorder caused by label misalignment, facilitates panel classification, and realizes automated panel production.
What Is a Lamello Invisible Connector Saw Blade? What Is Its Purpose?
The Lamello invisible connector is a type of hidden fastener used in furniture, serving as an alternative to traditional 3-in-1 connectors. Panels using this connector feature no visible holes, resulting in a more aesthetically pleasing appearance, while also offering simple assembly and stable structure.
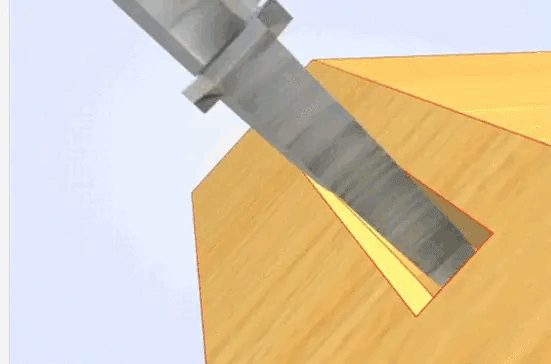
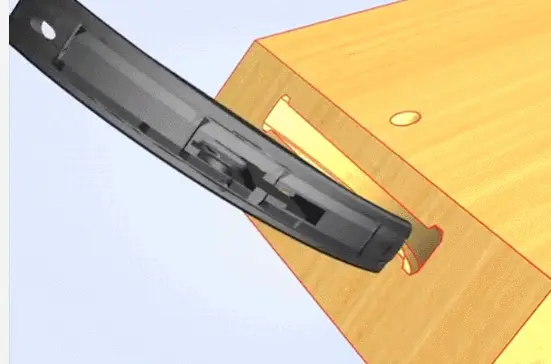
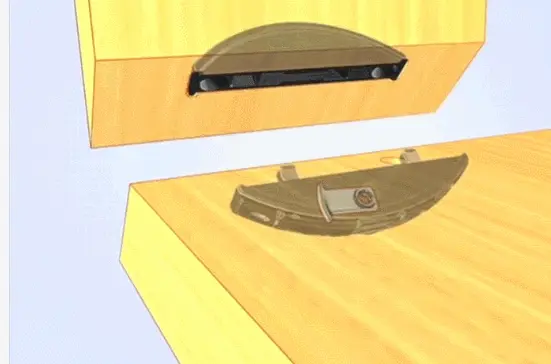
The CK-1328TA-DSL CNC wood router machine is equipped with a four-axis specialized grooving saw blade for Lamello connector , which can rotate freely at 90 degrees horizontally. This allows for quick cutting of sliding grooves in panels to accommodate the invisible connectors. Compared to traditional processing methods, this ensures more precise groove dimensions and faster processing speeds, effectively reducing connector wobble.
Features of the 4*9ft CNC Router for Furniture Woodworking Production Line
- 9KW automatic tool change (ATC) spindle, 18,000r/min, enables rapid cutting, grooving and milling of panels.
- Linear tool magazine holds 12 different tools simultaneously, automatically changing tools during processing to meet all panel machining requirements.
- 5+4 pneumatic drilling bank with 9 vertical drills for quick drill bit switching, efficiently handling batch drilling or multi-hole drilling operations to improve productivity.
- Lamello grooving saw blade driven by high-speed air-cooled spindle (18,000r/min), supports water cooling and 90° free rotation, ideal for complex groove processing.
- Automatic panel loading system handles multiple panels simultaneously, with height sensors that work seamlessly with labeling machine and vacuum suction loading system.
- Automatic labeling system applies labels before machining, automatically positioning and pressing labels onto surface for sorting and tracing.
- Conveyor unloading platform with automatic pusher transfers finished panels to discharge area.
- Annealed and aged heavy-duty bed ensures superior machine stability.
- Vacuum adsorption worktable with high-power vacuum pump features 8-zone/16-hole design, each zone with independent switch control for flexible operation.
- Double-rod pneumatic pressure rollers work with vacuum worktable to secure panels firmly, preventing movement during machining.
- 1500W bus-type absolute servo motors, XY axes equipped with Shimpo planetary gear reducers, achieving 80,000mm/min rapid speed with high positioning accuracy.
- Automatic lubrication system performs scheduled maintenance without manual intervention.
- EMC-shielded control cabinet houses all electrical components, effectively isolating electromagnetic interference.
- Dust collection system automatically collects processing debris for cleaner, more environmentally friendly operation.
- HIWIN 30mm linear guides/linear-motion bearing, TBI ball screws, and precision ground helical gear racks ensure 0.02mm repeat positioning accuracy.
- Syntec CNC system features intuitive multilingual interface, compatible with major CAD/CAM and nesting software, beginner-friendly operation.
Details of 4*9ft Atc CNC Router for Wardrobe and Cabinet Production
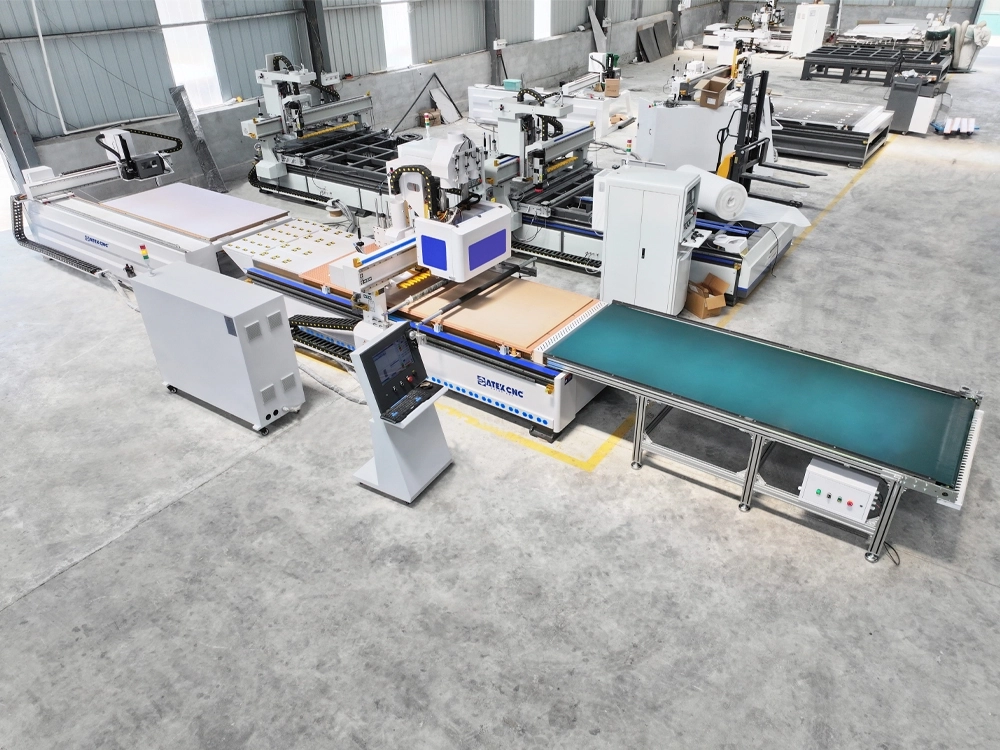
- Automatic labeling machine
The machine automatically applies labels to panels before processing, facilitating classification and traceability of finished panels.
- Loading vacuum suction cup
The suction cups are used to drag the panel from the lift-type loading platform to the worktable.
- Loading roller
During the loading process, the vacuum suction cups grip and transport the panel from the automatic lifting platform to the vacuum worktable. The loading rollers effectively reduce static friction during panel movement, ensuring smooth transfer and preventing panel damage.
- Double-rod pneumatic pressure roller
The double-rod pneumatic pressure roller and the vacuum worktable can quickly fix the plate.
- Vacuum zone control valve
Each vacuum adsorption zone is equipped with an independent control switch, enabling individual activation/deactivation of zones as needed to optimize power efficiency.
- ATC spindle, 5+4 pneumatic drilling bank, and Lamello grooving saw blade
Combine three functions to meet all processing requirements for wardrobe, cabinet, and other furniture production - including milling,drilling, cutting, grooving, profiling, engraving, and edge routing.
- Automatic tool setter
The automatic tool setter automatically performs tool tip position measurement and compensation calibration for tools of varying lengths after each tool change.
- Drive system
The system utilizes bus-type absolute servo motors for enhanced response speed and superior positioning accuracy. These motors eliminate the need for frequent homing operations during startup. When paired with planetary gear reducers, they enable faster machining positioning.
- Transmission system
The system incorporates HIWIN 30mm linear guides with matching sliding blocks, paired with ground helical gear racks and gears. The rack surfaces feature protective housings to ensure extended machine service life.
- Automatic lubrication system
Automatically lubricates the machine's entire transmission system to extend service life and maintain machining accuracy.
- Conveyor unloading platform
Automatically transfers processed panels from machining area to unloading zone via pusher mechanism, enabling continuous production without machine downtime.
- Taiwan's SYNTEC control system
Both control system and electrical components are equipped with independent cabinets to isolate electromagnetic interference, making the machine run more stably.
Technical Parameters of 4*9ft Automatic Multi-Function CNC Router Suitable for Mdf Furniture Processing
Model | CK-1328TA-DSL |
---|---|
XYZ Work Schedule | 1300*2800*200mm |
Gantry | Reinforced aged steel gantry, heavy-duty stress-relieved steel beam |
Bed | Machining center processing bed (heavy duty bed), independent anti-interference control cabinet |
Spindle | HSD 9KW air-cooled automatic tool change spindle |
Spindle Speed | 6,000-24,000rpm |
Tool Change Magazine | 8/12/16 linear tool magazine |
Collet | ISO30/ER32 φ20 |
Drilling Bank | HQD 5+4 pneumatic drilling bank |
Drilling Bank Speed | 4,500rpm |
Lamello Grooving Spindle | Dedicated high-speed air-cooled spindle for saw blades |
Lamello Grooving Spindle Speed | 18,000rpm |
Pressure Rollers | Double-rod pneumatic pressure rollers |
Table | Vacuum table 8 zones, 24 holes |
Positioning | 4+2 pneumatic positioning cylinders |
Tool Setting | Automatic tool setter |
Driving Mode | 1.5KW bus-type absolute servo motors (Z-axis with brake) |
Reducer | Shimpo (Japan) planetary gear reducers |
Transmission Mode | XY axis high-precision ground helical rack drive + Z axis high-precision TBI ball screw drive |
Guideway | Taiwan Hiwin high precision 30 linear square rail / linear-motion bearing |
Equipment Cable | Pure copper anti-bending high-flexible cable |
Dust Collection | 3KW dual-canister bag-type dust collector |
Vacuum Pump | 7.5KW water-ring vacuum pump |
Control System | Taiwan Syntec control system / Mach3 |
Lubrication System | Central lubrication oil filling maintenance system |
Pushing | Automatic pneumatic pusher |
Loading | Automatic lifting loading platform + labeling system |
Unloading | Conveyor-type automatic unloading platform |
Operating Voltage | AC380V 50/60Hz |
Engraving Instructions | G code |
Security System | Optical limit switches on XYZ axes |
Repeat Positioning Accuracy | ±0.02mm |
Maximum Pocessing Speed | 30,000mm/min |
Maximum No-Load Running Speed | 80,000mm/min |
Weight | 4500kg |
Dimensions | 11000*2300*2150mm |
What Products Can a 4×9ft CNC Router for Furniture Manufacturing Production Line Process?
Cabinets, wardrobes, tables, chairs, bookshelves, beds, nightstands, wine cabinets, TV stands, coffee tables, sofas, tatami platforms, computer desks, conference tables, filing cabinets, office furniture, display cabinets, cupboards, antique-style furniture, rosewood furniture, classical furniture, European-style furniture, bathroom vanities, solid wood doors, paint-free doors, craft wooden doors, screens, decorative windows, 3D wave panels, artistic relief carvings, solid wood doors, composite doors, cabinet doors, decorative windows, and various other furniture products.
Model | CK-1328TA-DSL |
---|---|
XYZ Work Schedule | 1300*2800*200mm |
Gantry | Reinforced aged steel gantry, heavy-duty stress-relieved steel beam |
Bed | Machining center processing bed (heavy duty bed), independent anti-interference control cabinet |
Spindle | HSD 9KW air-cooled automatic tool change spindle |
Spindle Speed | 6,000-24,000rpm |
Tool Change Magazine | 8/12/16 linear tool magazine |
Collet | ISO30/ER32 φ20 |
Drilling Bank | HQD 5+4 pneumatic drilling bank |
Drilling Bank Speed | 4,500rpm |
Lamello Grooving Spindle | Dedicated high-speed air-cooled spindle for saw blades |
Lamello Grooving Spindle Speed | 18,000rpm |
Pressure Rollers | Double-rod pneumatic pressure rollers |
Table | Vacuum table 8 zones, 24 holes |
Positioning | 4+2 pneumatic positioning cylinders |
Tool Setting | Automatic tool setter |
Driving Mode | 1.5KW bus-type absolute servo motors (Z-axis with brake) |
Reducer | Shimpo (Japan) planetary gear reducers |
Transmission Mode | XY axis high-precision ground helical rack drive + Z axis high-precision TBI ball screw drive |
Guideway | Taiwan Hiwin high precision 30 linear square rail / linear-motion bearing |
Equipment Cable | Pure copper anti-bending high-flexible cable |
Dust Collection | 3KW dual-canister bag-type dust collector |
Vacuum Pump | 7.5KW water-ring vacuum pump |
Control System | Taiwan Syntec control system / Mach3 |
Lubrication System | Central lubrication oil filling maintenance system |
Pushing | Automatic pneumatic pusher |
Loading | Automatic lifting loading platform + labeling system |
Unloading | Conveyor-type automatic unloading platform |
Operating Voltage | AC380V 50/60Hz |
Engraving Instructions | G code |
Security System | Optical limit switches on XYZ axes |
Repeat Positioning Accuracy | ±0.02mm |
Maximum Pocessing Speed | 30,000mm/min |
Maximum No-Load Running Speed | 80,000mm/min |
Weight | 4500kg |
Dimensions | 11000*2300*2150mm |
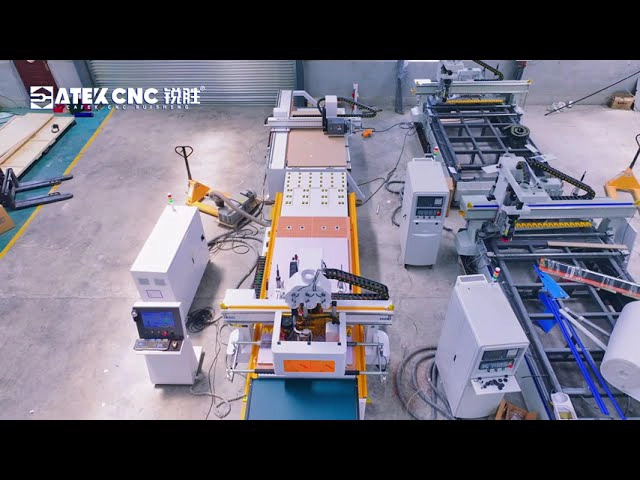
YOU MAY ALSO LIKE
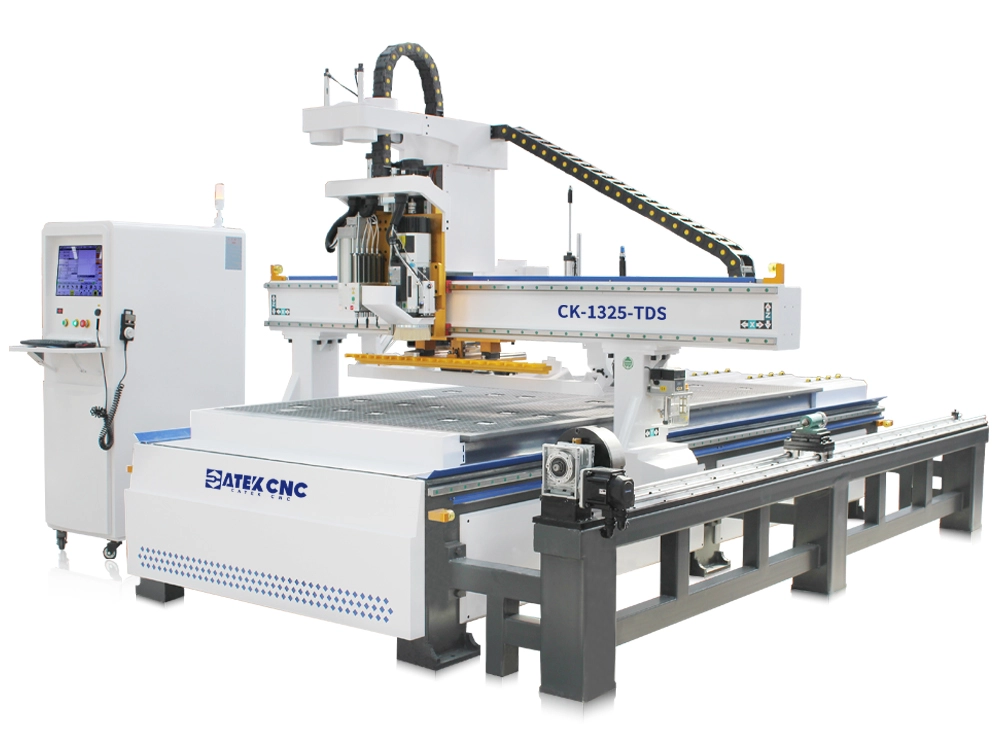
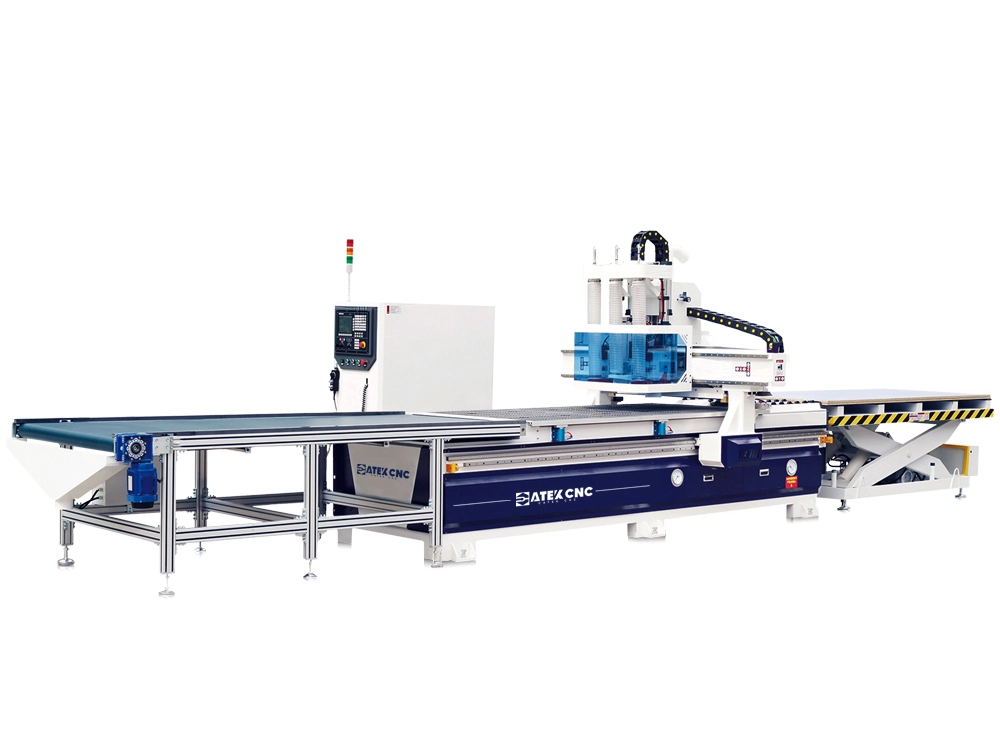
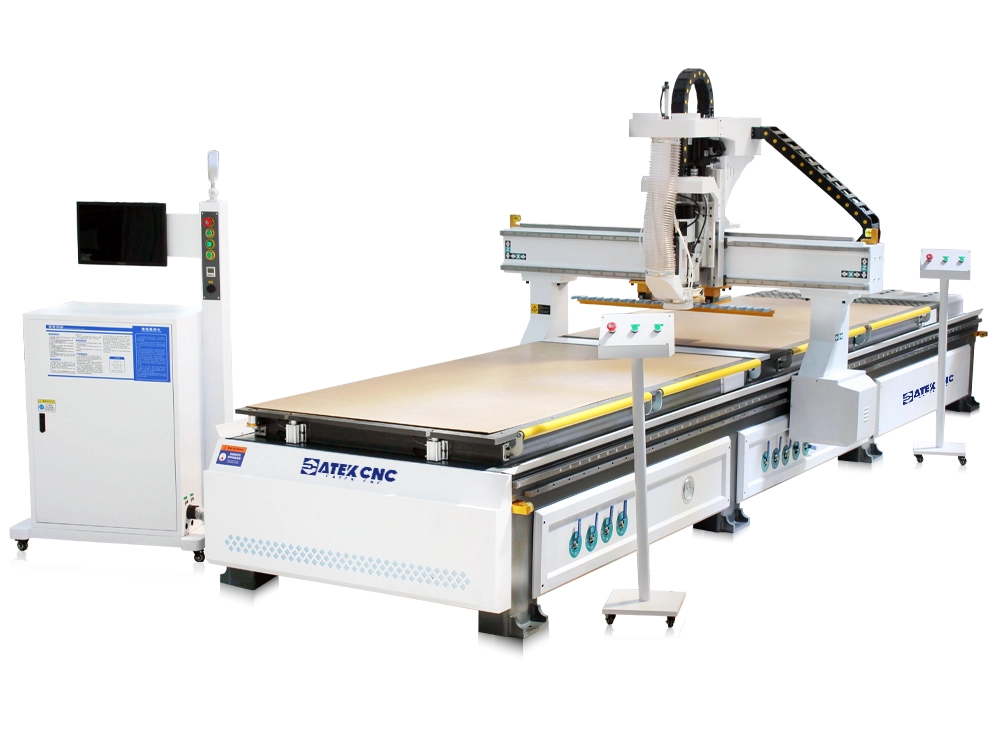
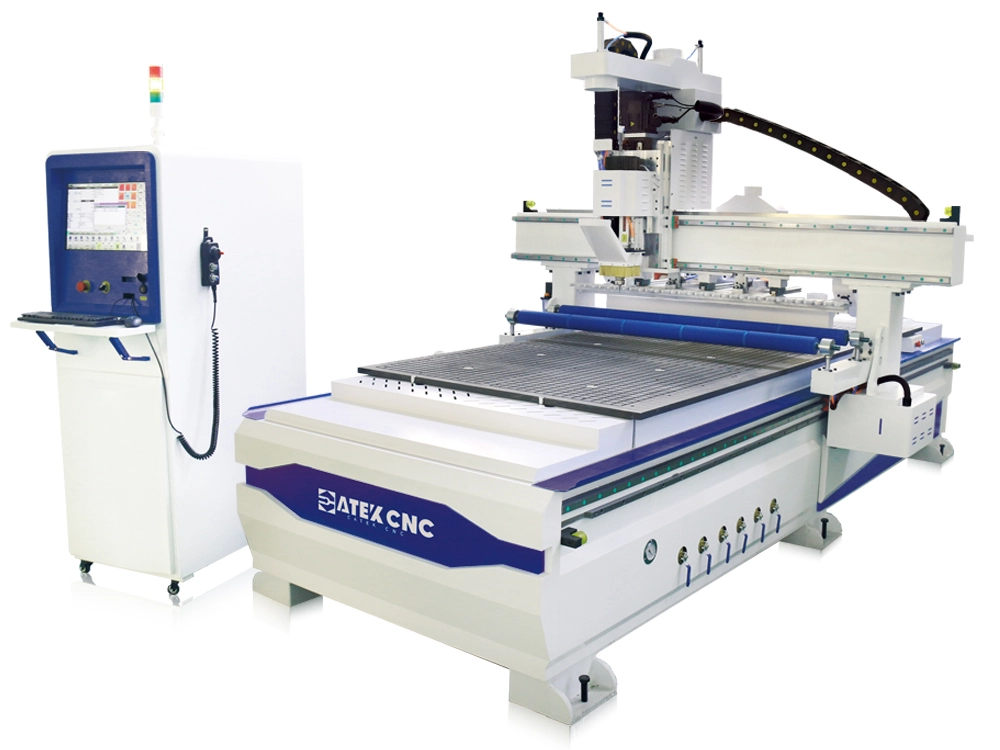

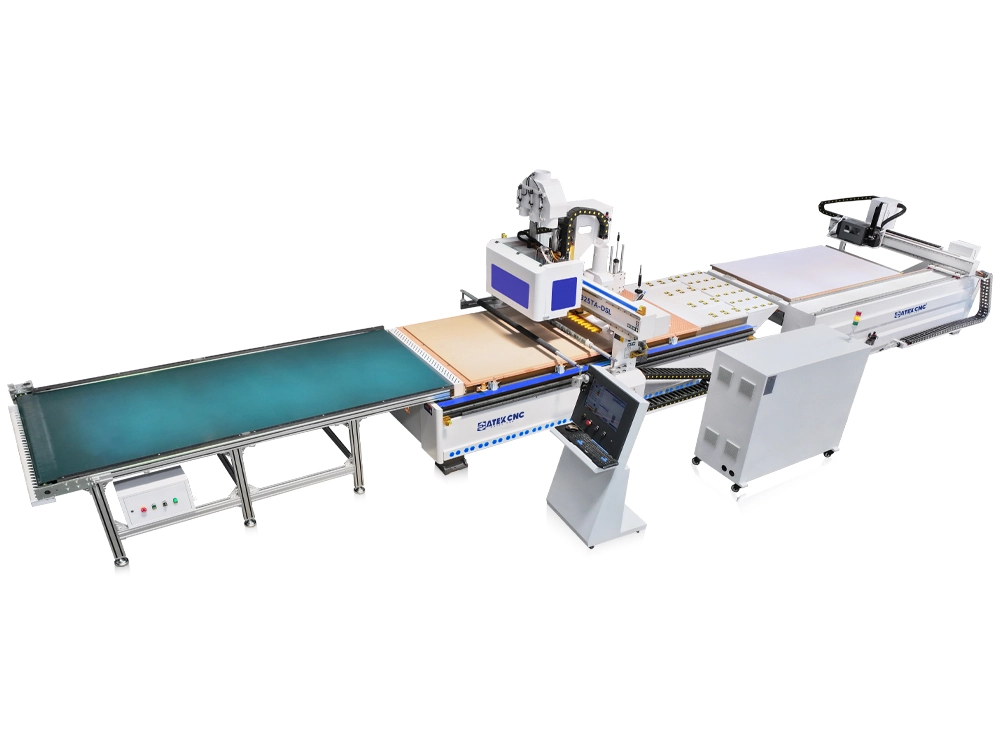
REVIEWS
Let more people know what you share.